Case Study
Recap: A customer planned two EV battery manufacturing facilities with complex and demanding production requirements. OTC identified compressor models that met the facilities' required output and developed a custom control system to monitor and manage their air needs.
Our Challenge
The growth of electric vehicles comes with a variety of opportunities and challenges. The need for high-quality EV batteries is a challenge faced by automakers, and as it’s a relatively new technology, there isn’t an exact blueprint for success. The construction of two massive EV battery manufacturing facilities was one company’s solution, and it turned to OTC Industrial Technologies to help get it done.
Battery manufacturing is complex. With many factors to juggle during production, there is very little room for error in this industry. Compressed air is one of the most essential resources for building EV batteries, but the amount of air required for the two new plants was massive.
Knowing they would need a one-of-a-kind solution for this undertaking, the facility designers turned to the experts at OTC and DIRECTAIR®. The compressed air usage for these facilities ranged from 20,000 to 100,000 cubic feet per minute (CFM). To meet this, massive compressors were required. Additionally, these compressors needed a steady source of air to maintain adequate pressure. If that wasn’t enough, the compressors needed to be smart enough to work in tandem with the countless other variables involved in battery production.
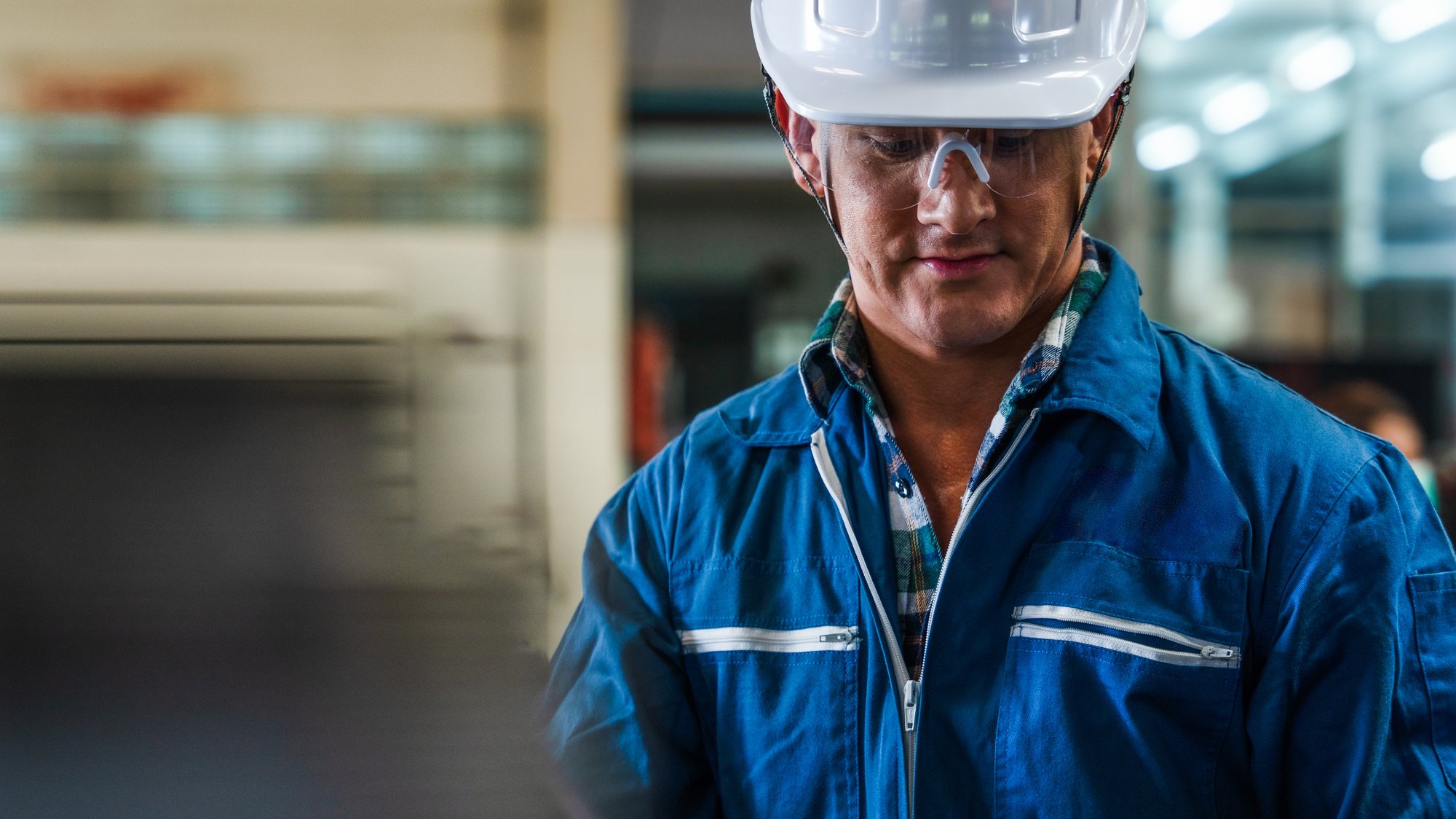
Our Solution
Understanding the size and importance of this challenge, OTC got to work. After meeting with the manufacturer, the team designed a compressed air solution and identified compressor models that would be able to match the stringent output requirements of each facility.
To ensure the system managed the precise compressed air requirements for production, OTC developed a custom control scheme. With the custom controls, the manufacturer has a seamless way to monitor and manage their compressed air needs. This system gives the customer control and visibility of the complex compressors, a necessity for efficient EV battery production.
OTC was able to design a custom, one-of-a-kind solution that worked for these innovative new facilities.
Results
Satisfied with OTC’s proposal, the customer accepted the plan. To help facilitate the construction of these facilities, OTC provided the manufacturer with a comprehensive plan to install each compressor. By taking the time to learn about the customer’s business and understand its unique needs, OTC was able to design a custom, one-of-a-kind solution that worked for these innovative new facilities.