Non-conformance costs in manufacturing can be extensive, covering scrap, rework, the cost of inspections and quality control, and more.
Our Challenge
A supplier and all-around manufacturer of pressed parts for the automotive industry struggled with a high scrap rate of non-conforming parts. This meant not only increased waste and higher production costs, but also extensive quality checks on every run.
Incorrect root cause analysis led to increased tooling repair and higher costs, but this work didn’t uncover a solution to the non-conformance.
The company was a long-time customer of OTC Industrial Technologies, so it turned to the Automation and Industrial Products team for help.
Our Solution
Working with the customer, OTC identified the root cause of the problem as incorrect nitrogen pressure levels in the equipment.
OTC installed a Fibro Wireless Pressure Monitor System (WPMS). This included installing sensors on the equipment itself and a gateway that could be used to remotely monitor nitrogen levels. This allowed the operators to monitor the nitrogen pressure levels before using the equipment. Nitrogen readings were then recorded by the operators before the press was used.
The new WPMS system allowed operators to monitor the tools either at the stamping press with an app, at any computer or device on the network, or remotely using an app on their phone. Nitrogen levels could be checked before work started, and then continually monitored during production. The WPMS automatically flagged any abnormality such as a leak or excessive heat before the failure of the work. This stopped scrap and allowed corrective action to be taken. In addition, the system automatically performed trend analysis to identify problem areas and flag equipment that may need repair or maintenance work.
Training of all the operators was then completed by the OTC team. Testing was done to ensure the new WPMS was working correctly.
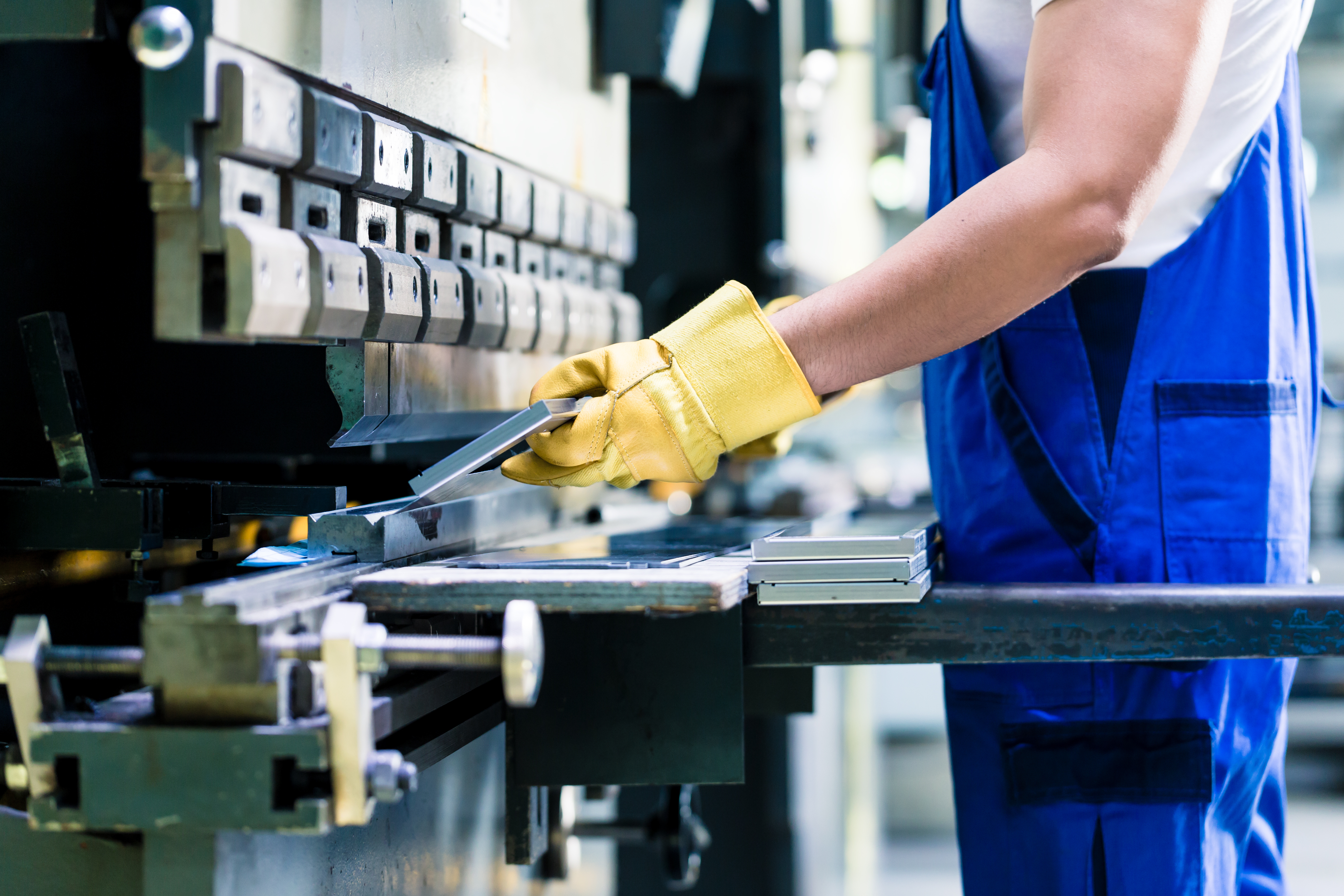
The Results
Today, the manufacturer has efficiently removed the root cause of form issues. Downtime and scrap from bad forms due to insufficient gas levels have both been eliminated.
Scrap due to insufficient gas levels has been eliminated.
The machine now automatically sends an alert and stops production at a failure occurrence. Maintenance technicians have been able to move to higher-priority work rather than repeating work due to insufficient gas problems. The labor requirements for quality technicians have been reduced so they could be moved to other work.
In addition, the WPMS has greatly increased productivity at the plant. Prepping for a job once took up to 10 minutes per set of tools, with as many as 300 tools. Today, that work takes only seconds using the WPMS.
Due to the success of the solution, the customer is implementing the system at its plants across the world, making the WPMS standard on all new models with nitrogen gas springs.