According to studies, processed energy costs like electricity have increased as much as 34% in recent years.
Our Challenge
Cardington Yutaka Technologies, Inc. (CYT) is an Ohio automobile parts manufacturer specializing in torque converters, catalytic converters, and exhaust systems. In addition to the main production facility, CYT has two satellite facilities on site, including a remanufacturing plant and a smaller plant with limited shifts.
For compressed air in the remanufacturing site, CYT operated two 100-horsepower (HP) air compressors. The air compressors were able to meet the demand at the plant at 60% capacity. This meant higher energy costs and wasted capacity. Because the compressors were older and inefficient, they required frequent, high-cost maintenance and repairs.
At the other, smaller plant outside the main facility, CYT was using a rented 25HP air compressor with a desiccant dryer. The older refrigerant dryers at the plant were no longer operable. This desiccant dryer wasn’t designed for the system, causing inefficiencies and increased energy costs.
The managers at CYT asked the experts at OTC to evaluate the air compressor systems at the plant and to provide options.
Our Solution
After conducting a thorough evaluation of the site, including the compressed air systems, the conditions at the plants, and the compressed air requirements, the team at OTC suggested running an underground pipe between the two plants. This would provide energy efficiency and reliable compressed air at the sites. In addition to the pipe, CYT would remove the old, inefficient 100HP compressors and the 25HP rental unit and move to the DIRECTAIR® compressed air utility service.
OTC and the DIRECTAIR® team installed a new compressed air facility at the CYT site. This included three 75HP air compressors as well as a compressed air monitoring system.
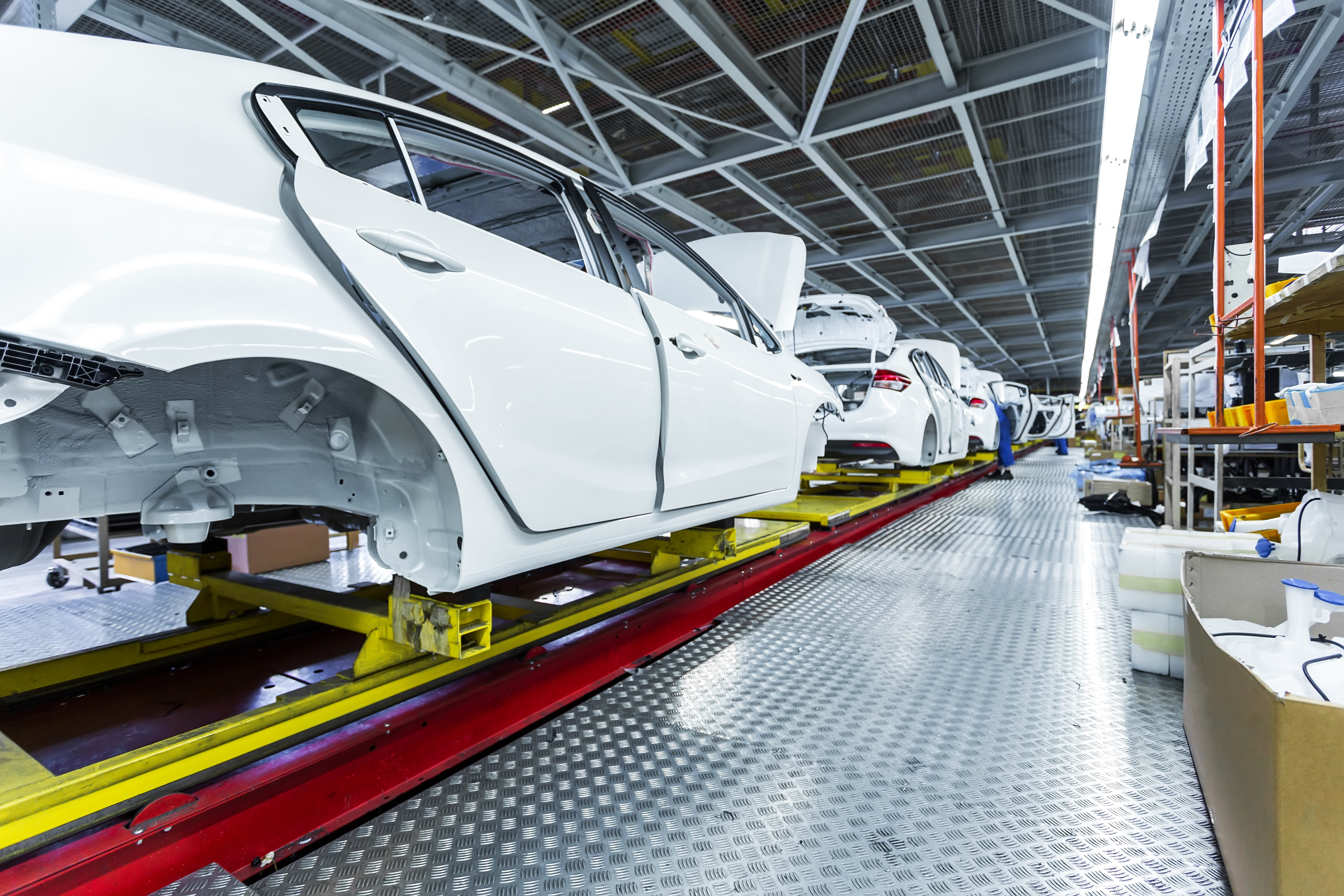
The Results
OTC and the DIRECTAIR® team manage, operate, and maintain the new compressed air system for CYT, while CYT focuses on production. With DIRECTAIR®, CYT receives a monthly bill only for the compressed air it uses; otherwise, it pays no maintenance, upkeep, or capital costs for the system.
The manufacturer expects to save more than $200,000 in energy costs in the next eight years.
With DIRECTAIR®, CYT enjoys continuous clean, dry air; 100% reliability; optimal energy savings; and 24/7 support from the OTC team. By eliminating CYT’s maintenance and repair costs, excessive energy costs, ongoing rental costs, dryer purge losses, and the internal labor needed to keep the system operational, CYT expects to save more than $200,000 over the next eight years.