A longtime customer in the food and beverage industry worked with the OTC team for motor repairs and purchases. Over that time, the company had come to rely on OTC for emergency repairs.
The customer had a catastrophic failure of its ammonia compressor motors focused on beef refrigeration at one of its facilities and immediately turned to OTC for help.
OTC capabilities:
- Food and beverage industry experience
- Equipment repair
- Dedicated repair and maintenance teams
- Dedicated repair shops
Eight motors and ammonia compressors went down, with the potential of costing the company millions in revenue.
Our Challenge
At one of its food and beverage production facilities, this customer used large ammonia compressor motors for beef refrigeration. There were several compounding failures that took down the system, including misalignment, rotor dragging on the stater, and power disruption due to storms. All told, eight motors and ammonia compressors went down: four 700hp, two 500hp, and two 250hp.
The motors cooled beef products sold worldwide, and the catastrophic failure had the potential of costing the company millions in lost revenue.
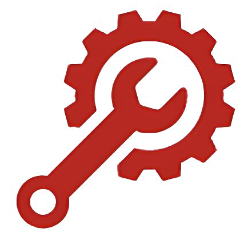
Our Solution
Upon investigation, the customer’s initial solution was to purchase 700hp medium voltage motors, which are usually readily available. However, due to supply chain issues, manufacturers were quoting a 50-week lead time. With the need to get the refrigeration units operating rapidly, the OTC team checked the secondary market for refurbished motors without any luck.
OTC then proposed repairing the existing motors as quickly as possible. The next day, the motors were removed, and after an initial review, it was determined the compressor motors weren’t aligned correctly. OTC's Service & Repair technicians were able to get some of the motors up and running.
For the remaining motors, OTC worked with the customer to identify the most crucial components and prioritize those repairs. Extra couplings and bearings were pre-ordered to prevent delays. Work on the motors was spread to additional OTC service shops to ensure it could be completed as quickly as possible, with technicians and winders working overtime and on Sundays to get the work done.
With the plan in place, OTC was able to complete the repair work and return the critical 700hp motors to service in just two days.
With OTC's creative solution, the repair was completed in just two days, saving the manufacturer from significant downtime.
The Results
After the rush repair work by OTC, the motors are running extremely well.
To prevent future problems, the customer is having the alignment checked periodically. The OTC techs review the motors, identifying ones that may need attention to prevent future problems or catastrophic breakdowns.
The customer was genuinely thankful and thrilled that OTC delivered results and solutions in such a short time.