Catastrophic failures cost $4,000 a day in downtime and $75,000 a year in repairs
Our Challenge
A food and beverage manufacturer used boiler feed water pumps on two production lines, including two boilers with three identical 425gpm at 400 PSI feed water pumps. The boilers had different steam flow rates, feeding two production lines that had different steam flow requirements depending on the process. The steam flow requirements could vary from 55,000 lbs./hour to as much as 200,000 lbs./hour.
With so much use on the boiler feed water pumps, the manufacturer was having frequent catastrophic failures. The failures cost the company as much as $75,000 a year in equipment and labor to repair, on top of the $4,000 a day in downtime for each line.
The manufacturer, a long-time customer of OTC, needed an analysis of the steam usage between the two lines.
Our Solution
The OTC team spent a week at the facility, taking steam flow and water readings as well as documenting the steam requirements of each line. This included recording the motor amperage and suction and discharge pressure readings at the pumps in different scenarios, and monitoring the deaerator tank levels and temperatures.
Using the data, the team ran scenarios of all the possible steam flows for the lines. The goal was to find the optimal configuration for the pumps, boilers, and steam flow.
After the analysis, OTC recommended replacing one of the 425gpm pumps with two 200gpm pumps.
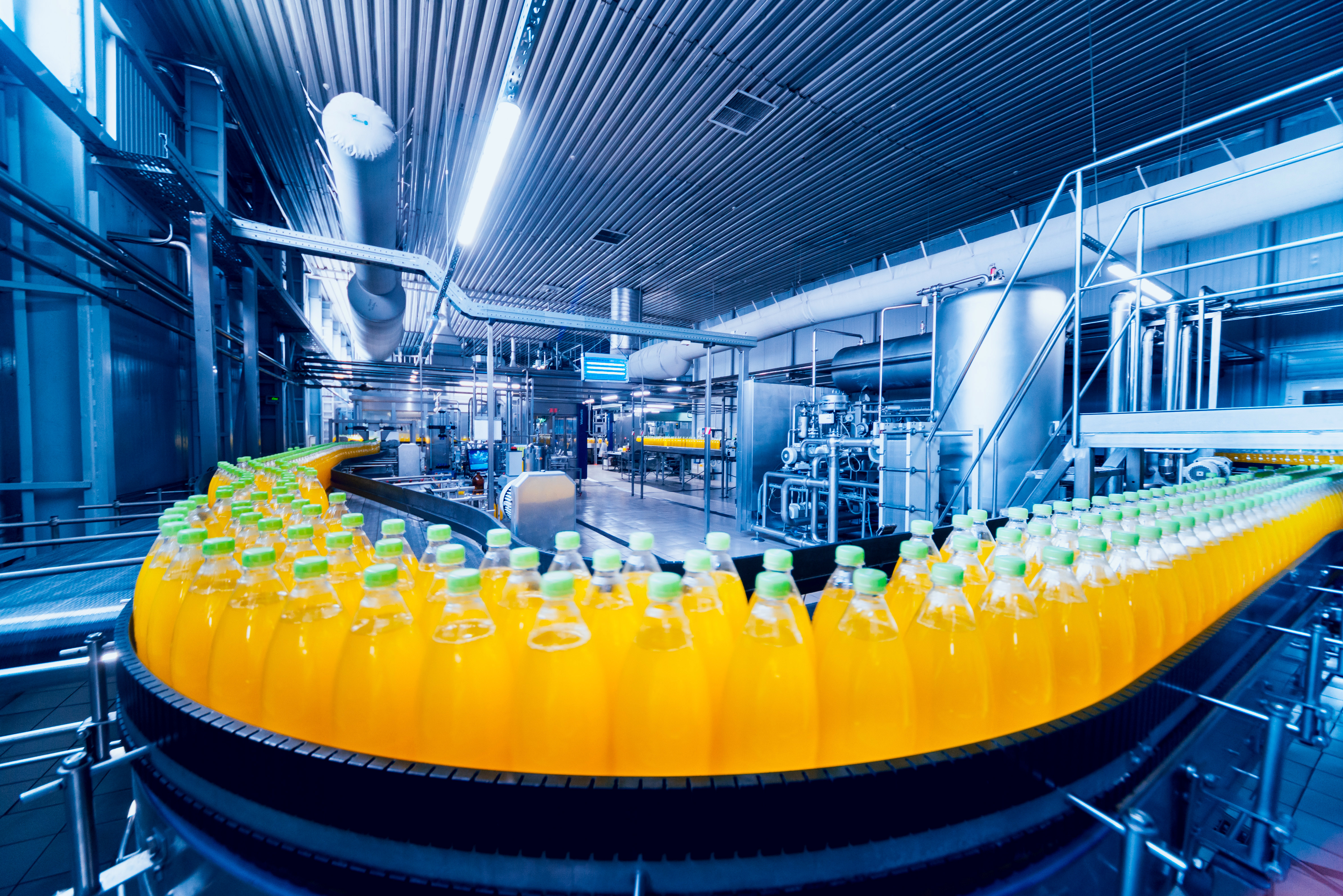
The Results
At OTC’s recommendation, the manufacturer did purchase the two new smaller pumps. With the new pumps in place, the customer reconfigured how the boiler feed water pumps operate.
For processes up to 100,000 lbs./hour, the two smaller pumps run. For processes that require more than 100,000 lbs./hour, the single larger pump runs. In addition, the other larger pump is available as a spare.
The OTC solution saves $250,000 a year in energy savings and the elimination of associated repair costs and downtime.
Now that the company isn’t running a pump that is too big for its steam flow requirements, the new pump configuration saves approximately 40% on its system energy costs. With the additional savings it sees from a more reliable boiler feed water pump system, the facility estimates it is saving approximately $250,000 a year.