Case Study
Recap: An innovative furniture company sought to reduce power costs and increase uptime for its air compressor systems
Our Challenge
A furniture company had six air compressors operating in three separate plants. Each machine was running only partially loaded. Although two of the plants were connected, the combined air compressors were operating as two separate systems.
The complexity of the air compressor needs across the plant network was creating pressure issues that had a negative impact on production and production quality. It also led to wasted pressure and higher energy costs.
Recent studies show manufacturers spend more than $200 billion each year in energy, and 30% of that is wasted.
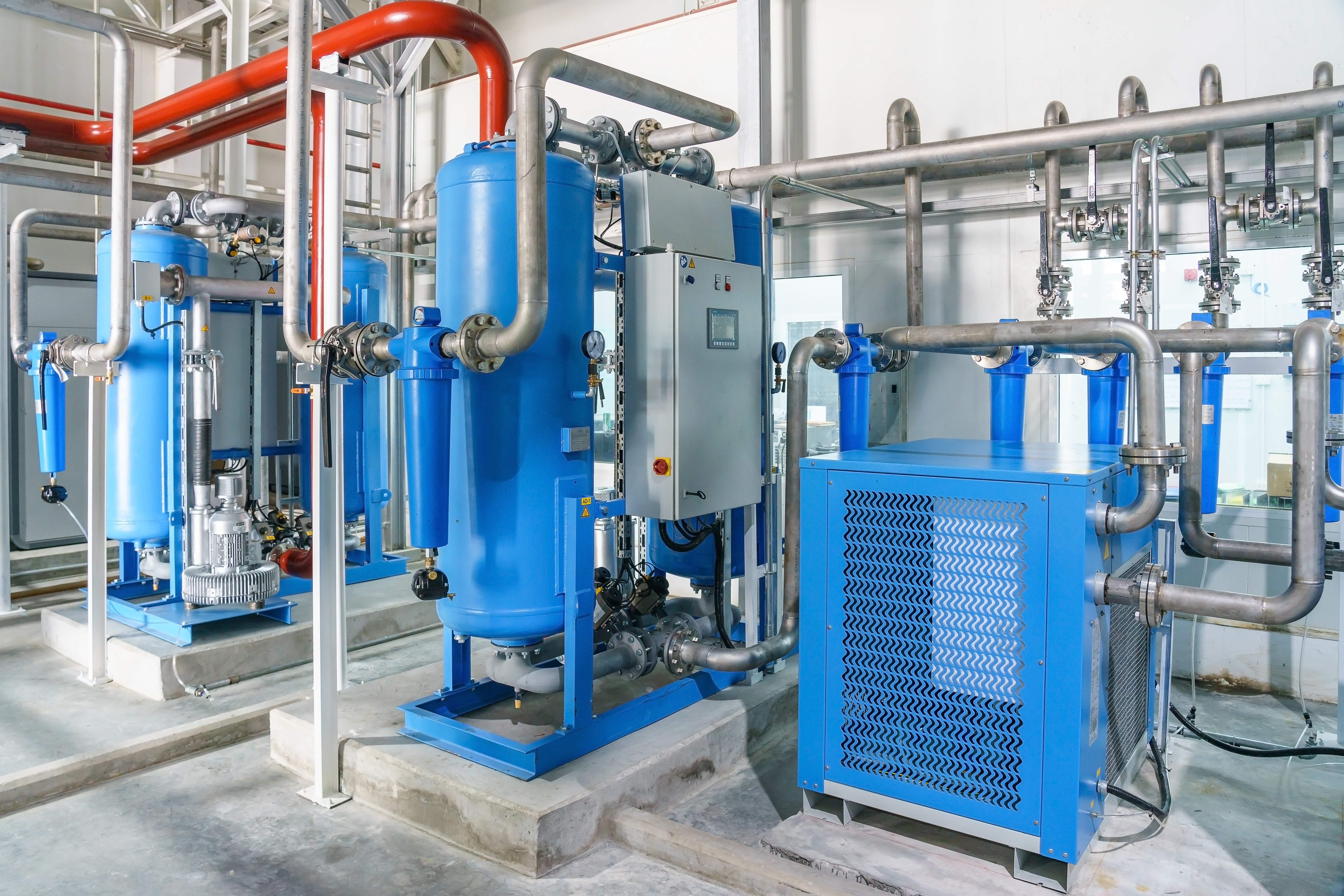
Our Solution
The furniture manufacturer contacted DIRECTAIR®, an OTC Industrial Technologies product, for help. After a plant walkthrough and a two-week on-site air audit of the company's compressed air systems, the team suggested a solution. The MANAGAIR® monitor and control system would optimize pressure across the six air compressors.
MANAGAIR® is a state-of-the-art computerized system that centrally monitors and controls a compressed air system 24 hours a day. With the system, the company could maintain the air compressors at peak efficiency, saving energy costs and ensuring continual uptime and optimal air pressure for operations.
In one year, the manufacturer saw cost savings of almost $75,000
Results
After installation, OTC was able to operate the two connected plants as one system with no issues and monitor all compressor systems via MANAGAIR®. It solved all pressure issues with a pressure band of 5 psi.
With optimal operation efficiency, the MANAGAIR® system now saves about $75,000 in energy costs annually. Additionally, the manufacturer applied for and received an energy rebate providing an additional $13,375 in savings.