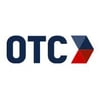
OTC Insights Team
Established in 1963, OTC Industrial Technologies (Ohio Transmission Corporation) is one of the largest industrial distributors & service providers in the United States. We're committed to seeing industrial operations advance through expert technical solutions & unmatched support using our years of experience.
Imagine having a service in your back pocket that is continually monitoring your machines so you don’t have to. How much efficiency would you see if a team of experts was constantly reviewing the status of your machine utilities, making sure everything was operating optimally, and stepping in when a problem occurred to prevent a line shutdown or an expensive breakdown?
Enter MONITAIR®.
Compressed air systems can wear down over time from improper inspection and awareness, causing machines to break down more often. Problems can occur that can impact output and utility, costing you money, but you may not even know it’s happening.
This increases operational expenses and can lead your business into wasting money on poorly maintained machines. It can even sap into your efficiency and productivity on the floor.
There are solutions. MONITAIR® is designed to help your manufacturing facility run more smoothly and efficiently by monitoring compressed air operations.
What is MONITAIR® Compressed Air Service?
Like having an expert air compressor technician on standby, MONITAIR® watches your machines 24 hours a day. It’s an advanced monitoring system for compressed air operations, providing vital data on output and performance. Benchmarks and operation triggers provide alerts at the first sign of a problem, and data allows OTC experts to customize settings for better performance and greater energy efficiency, and cost savings.
Through remote monitoring, your compressed air system will be protected to ensure it runs at optimal speeds to increase efficiency and reliability over the long term.
What do MONITAIR® services do for you?
When you sign up for MONITAIR® services, you can expect:
-
Communication 24/7
With around-the-clock surveillance, our MONITAIR® system will direct the important air compressor data to our expert service team for fast support and expert attention.
-
Precise analytics
With multiple channels in the data collection process, your compressed air system will have its problems dealt with in real-time. You have a complete picture of air compressor performance. This allows for a proactive approach which can prevent downtime during normal working hours.
-
Reliable service contracts
Machine maintenance performed on one of our client service contracts ensures that repairs, replacement, and quality checks are done on an “as needed” basis. That way, maintenance costs are reduced and time spent working on machines can be more efficient. You have reliable operations and can focus on higher-priority tasks.
Why choose MONITAIR®?
MONITAIR® can protect your machine preemptively so you can focus on more pressing matters for your business. Customers report several benefits moving from an in-house air compressor utility to DIRECTAIR® and MONITAIR®, including:
-
Convenience
Being an online service, MONITAIR® has remote access to your compressor 24 hours a day, seven days a week. If anything goes wrong, it will be known immediately.
-
Unmatched reliability
With being trusted advisors in the Midwest for years, OTC’s MONITAIR® services come with reliability built in. As one of the largest factory-trained service teams, our technical experts can handle any obstacle.
-
Increased productivity
On the factory floor, even one machine down could hurt the bottom line. Our dedicated experts ensure that your air compressor is operating at optimal pressure, temperature, speed, and performance.
-
Cost-effectiveness
By minimizing, or even eliminating, unscheduled downtime, MONITAIR® can save you from unexpected costs and expenses. If a problem does occur, the experts at OTC can relay instructions by email, text, or phone, so maintenance can be performed as quickly and efficiently as possible.
-
A boost in efficiency
With built-in trending functions and data analysis capability, MONITAIR® logs all relevant data to your database, allowing us to diagnose and solve many of the most common air compressor problems and identify opportunities for optimization.
The future of compressed air
MONITAIR® brings a host of possibilities and opportunities to the care and maintenance of your compressed air system. Rather than leave your air utility up to chance, leverage the latest monitoring technology for your production with MONITAIR® and OTC’s innovative DIRECTAIR® service.
OTC is proud to offer this service and a myriad of other air technology services to its customers, making us the complete solution for your air technology needs.
Contact OTC today to get started.
Stay up to date
SUBSCRIBE TO OUR BLOGPosts by Tag
- General Manufacturing (99)
- Compressed Air Solutions (54)
- Automotive (35)
- Finishing and Dispensing (31)
- Rotating Equipment (27)
- Industrial Automation (21)
- Maintenance & Repair Services (20)
- Case Studies (15)
- Electronics & Semiconductor (14)
- Sustainable Manufacturing (11)
- Energy Efficiency (10)
- Filtration (8)
- Energy, Power & Utilities (7)
- Food & Beverage (5)
- Oil & Gas (5)
- Pharmaceutical & Life Sciences (4)
- Industrial OEMs (3)
- Steel & Metal Manufacturing (3)
- Aerospace (2)
- Agriculture (2)
- Chemical & Petrochemical (1)
- Packaging & Processing (1)