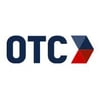
OTC Insights Team
Established in 1963, OTC Industrial Technologies (Ohio Transmission Corporation) is one of the largest industrial distributors & service providers in the United States. We're committed to seeing industrial operations advance through expert technical solutions & unmatched support using our years of experience.
Manufacturers can see measurable and sustainable production and operational efficiency improvements with accurate data and the right information.
Unfortunately, many businesses still struggle to make efficiency improvements. Instead, they work with reports that only provide a glimpse into the past, then scramble to fix problems as they happen. Identifying and using KPIs is the first step in overcoming the struggle and making sustainable improvements.
What Are KPIs?
Key performance indicators (KPIs) are high on the wish list of many manufacturers.
KPIs are quantifiable performance measurements. They focus on a specific objective for the business. Using them, you can:
- Track progress toward meeting a goal.
- Set triggers to flag a potential problem.
- Identify opportunities for improvement.
As beneficial as KPIs are for manufacturers, many companies struggle to use them. They may not have the ability to collect accurate and timely data. Other companies may not be tracking the right KPIs. They may not understand how the data can increase production efficiency. They have the data but aren’t sure how to use it.
In this article, we’ll cover a few critical KPIs that can help increase efficiency. We’ll also look at what the data means as you consider potential efficiency improvements.
Critical KPIs for Production Efficiency
One area that seems to create problems for manufacturers as they evaluate KPIs is the data they need. Some companies are reluctant to measure data and so have very few KPIs they use. This leaves production leaders with very little visibility into production efficiency. Other companies mistakenly believe that more data is always better. They end up drowning in reports, using none of them.
A better strategy is to use your business or production goals as a guideline for the KPIs you track. Identify the KPIs that measure your progress toward the goal and make them alone the focus of your data strategy.
The KPIs below are critical measures for production efficiency and can be used as you plan and implement a strategy for improving efficiency.
Production Volume
This KPI measures the units or products manufactured over a specific time. For example, how many units completed production over a day (24 hours). It is the primary benchmark for tracking production efficiency and provides insight into the overall output of your production team.
Production volume = Total units manufactured over a designated time
Once you have a baseline of production volume, you can track deviation over or under that baseline. Changes in volume can be tied to changes in production, for example, a machine going down, slow sales, or a labor issue.
On-Time Delivery
Production volume is only the starting point for tracking efficiency. Another data point is on-time delivery. This measures the percentage of orders delivered successfully and on time to customers.
On-time delivery = Units delivered on time / total units delivered
While production volume provides insight into the total output, on-time delivery incorporates late and catch-up production in the data. This KPI shows if the work being done is planned or if it is compensating for other production issues like scheduling problems or previous production delays.
Unit Cost
Another name for this KPI is Cost of Goods Sold (COGS). It provides an average of the cost to produce one unit.
Unit cost = Fixed cost + Variable cost / Production volume
Efficient production should limit the variation in the unit cost. Any increase or decrease in unit cost would mean that a change in production efficiency has occurred. Often, an increase in production will mean an increase in waste, which can be an overall decrease in production efficiency.
Overall Operations Effectiveness (OOE)
Like OEE (Overall Equipment Effectiveness), OOE calculates the percentage of time your production team spends delivering products at quality. It factors performance or the percentage of time that the production team (including machines) is operating at total capacity. It includes quality or the percentage of units that are produced without defects. Finally, it looks at availability or the percentage of time in which production occurred. Unlike OEE, maintenance is included in availability as it is vital to efficient production.
Overall Operations Effectiveness = Performance x quality x availability
Typically, you can use OOE to compare production areas or equipment in the plant to see how efficient each is. Areas with a higher OOE can be used to benchmark other areas, building best practices to increase overall efficiency. You can also use it to identify areas that are creating potential production bottlenecks.
Capacity Utilization
Capacity utilization looks at the plant's availability of capacity for production. Think of it like an overall OOE for the entire plant. It is a key measure of overall efficiency.
Capacity utilization = (Total Capacity used over a designated time / total available capacity) x 100
Over time, as efficiency increases, capacity utilization should increase, showing business growth and growth potential. A decrease in capacity utilization could be a sign of decreased sales or a problem with efficiency which will slow growth. An increase means that production may be at higher risk if there is downtime in an area.
Using KPIs for Improving Efficiency
Utilizing KPIs to guide efficiency improvement and track progress toward goals can initially be confusing and intimidating. In manufacturing, the focus is on production. Spending time poring over KPI dashboards and planning for improvement doesn’t get more products out the door. In addition, that planning doesn’t provide a guaranteed return.
There are benefits. An increase in efficiency is necessary for business growth. Improving efficiency is worth the time and effort.
Keep in mind that resources are available to help you set KPIs or implement improvement strategies. If you see a problem with efficiency, whether it’s a pump that goes down frequently or difficulty in capturing data, then you should bring in an outside expert like the team at OTC. Frequently, the challenge preventing optimal efficiency can be overcome with the support and expertise of an end-to-end solution provider like OTC.
Don’t wait to optimize and improve your production efficiency. Contact OTC today for a no-obligation consultation. Let’s see what we can do to support you.
Stay up to date
SUBSCRIBE TO OUR BLOGPosts by Tag
- General Manufacturing (99)
- Compressed Air Solutions (54)
- Automotive (35)
- Finishing and Dispensing (31)
- Rotating Equipment (27)
- Industrial Automation (21)
- Maintenance & Repair Services (20)
- Case Studies (15)
- Electronics & Semiconductor (14)
- Sustainable Manufacturing (11)
- Energy Efficiency (10)
- Filtration (8)
- Energy, Power & Utilities (7)
- Food & Beverage (5)
- Oil & Gas (5)
- Pharmaceutical & Life Sciences (4)
- Industrial OEMs (3)
- Steel & Metal Manufacturing (3)
- Aerospace (2)
- Agriculture (2)
- Chemical & Petrochemical (1)
- Packaging & Processing (1)