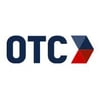
OTC Insights Team
Established in 1963, OTC Industrial Technologies (Ohio Transmission Corporation) is one of the largest industrial distributors & service providers in the United States. We're committed to seeing industrial operations advance through expert technical solutions & unmatched support using our years of experience.
Paint booths are a big investment.
With many moving parts that could increase efficiency or cause a problem, your paint booth could either be an asset or a liability. As a complex piece of equipment, keeping your paint booth effective will reduce safety hazards, maintain regulatory standards, and ensure a quality product.
One of the key factors to accomplishing this is prioritizing paint booth filter maintenance.
Discover from OTC what paint booth maintenance is and tips to ensure filter maintenance within your paint booth.
What Is Paint Booth Maintenance?
Paint booth maintenance is the process of keeping your booth clean, effective, compliant, and safe.
With many projects running through a paint booth, one that's in poor condition could result in expensive repairs or machine replacements, hazardous working conditions, increased cycle times, unhappy customers, and even code violations.
Importance of Paint Booth Filter Maintenance
Filter maintenance in your paint booth is critical for longer lasting equipment, less expensive upkeep, a safer working environment, and increased productivity and efficiency. Filters prevent unwanted substances from getting into the paint booth or being released into the environment. Those filters only work if they are properly and continuously monitored and are replaced when dirty or old.
Here are six tips to secure paint booth filter maintenance.
1. Create a Paint Booth Maintenance Schedule
Prevent filter problems by establishing a paint booth maintenance schedule. Set guidelines for monitoring, cleaning, and replacing filters (when necessary). This will ensure that your booth is operating at optimal levels and operation managers have a demonstrated history of scheduled maintenance on record for any mishaps or machine repair needs.
2. Clean the Paint Booth
A clean paint booth is a safe paint booth. Overspray can build up along the walls and other interior areas from project to project, collecting dust and other particles that can make it difficult for workers. It can also leave a residue on products that customers will notice. Cleaning the interior from wall to floor daily will ensure better working conditions and a quality finish on products in the paint booth.
3. Choose the Right Filter
Filters are not all made the same. Make sure you have filters that are right for the job they are performing. Replacing a filter with one that isn’t made for the intended use could damage your paint booth. Here are the most common paint booth filters and their uses:
- Air makeup filters: Picking out large contaminants from the air, these filters remove dust within the air makeup before it can get to the paint booth. Purchase air makeup filters from OTC right here.
- Exhaust filters: Helping to keep hazardous chemicals from being released outside of the paint booth, these filters catch toxins leaving the paint booth. Purchase exhaust filters from OTC right here.
- Intake filters: Keeping substances away from the coating, these filters can be found in cross-draft and downdraft booths. Purchase intake filters from OTC right here.
4. Review Regulations for Your Paint Booth
Check with machine manuals and manufacturing regulations to ensure your paint booth and its filters are code compliant and up to date. Regulations are in place to protect machines, employees, and your business. Noncompliant machines and processes can lead to unsafe work conditions, violations, and fines.
5. Schedule Time to Replace Filters
Clogged filters decrease airflow and can damage paint booth components like exhaust fans. Clogged filters can also lead to lower productivity, extra cleaning, and labor before and after projects. Replacing filters on time and correctly will prevent problems and keep a free flow of clean air going in and out of the booth.
6. Safely Dispose of Old Filters
Knowing the life cycle of each type of filter and the proper disposal techniques is important to keeping workers and the environment safe. At a minimum, put an old filter in a plastic bag with minimal shaking, then dispose of it in an outside trash can. When replacing filters, do not leave any piece of equipment without a filter.
Partner with OTC for Your Finishing Needs
Many of the steps here seem simple, but they are critical to safe operation of a paint booth and high-quality results for your products. If you have questions, OTC can help. We’ll help you finish a product right to leave your customers happy with a quality product and flawless finish.
Talk with a finishing expert at OTC. We’ll analyze your current system to identify opportunities to be more efficient, productive, and more economical long term. Get in touch with an expert today.
Stay up to date
SUBSCRIBE TO OUR BLOGPosts by Tag
- General Manufacturing (99)
- Compressed Air Solutions (54)
- Automotive (35)
- Finishing and Dispensing (31)
- Rotating Equipment (27)
- Industrial Automation (21)
- Maintenance & Repair Services (20)
- Case Studies (15)
- Electronics & Semiconductor (14)
- Sustainable Manufacturing (11)
- Energy Efficiency (10)
- Filtration (8)
- Energy, Power & Utilities (7)
- Food & Beverage (5)
- Oil & Gas (5)
- Pharmaceutical & Life Sciences (4)
- Industrial OEMs (3)
- Steel & Metal Manufacturing (3)
- Aerospace (2)
- Agriculture (2)
- Chemical & Petrochemical (1)
- Packaging & Processing (1)