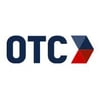
OTC Insights Team
Established in 1963, OTC Industrial Technologies (Ohio Transmission Corporation) is one of the largest industrial distributors & service providers in the United States. We're committed to seeing industrial operations advance through expert technical solutions & unmatched support using our years of experience.
Maintaining your paint booth filters is integral to keeping your paint booth running smoothly and efficiently.
If you don’t change your filters regularly, you increase your risk on every project. Decreased airflow and increased paint contamination are common with a dirty filter, which can lead to poor-quality project finishes, angry customers, damage to your equipment, or even unsafe working conditions.
In this article, we’ll cover the importance of setting up a maintenance schedule for your paint booth filters. We’ll cover expert tips on how to conduct maintenance so you can safeguard your tools and equipment, increase efficiency, and protect finish quality. We’ll also discuss the importance of consulting with an expert before switching your filter style or brand.
How to Schedule Paint Booth Filter Changes
One of the essential aspects of paint booth filter maintenance is setting up a regular change schedule.
The type of paint you are using, the size of your booth, the filter, and the products being painted will have an impact on the frequency of filter maintenance. A higher volume of work will require more frequent filter replacement, for example.
It’s important to consult with an expert to determine how often you should be changing your filters, and if there is a better filter option on the market. Using a higher or lower quality filter, or the wrong filter, can cause problems like a clogged applicator. An expert can evaluate your current processes and equipment, and then provide best practices that will be the foundation of your schedule.
Once you have determined how often to change your filters, you’ll need to set up a paint booth filter change log. The log will help you keep track of when you changed your filters and what kind of paint was being used at the time.
Setting Up a Paint Booth Filter Change Log
A paint booth filter change log has many benefits and is critical for your paint or spray booth maintenance.
First, it allows you to keep track of when you need to change your filters, preventing any mistakes that can lead to paint contamination, decreased airflow, or worksite safety problems.
The change log also enables you to identify trends in your paint usage that may be causing increased filter changes. For example, if you notice that you are changing your filters more frequently when using certain types of paint, you can adjust your process accordingly.
Finally, a paint booth filter change schedule can be a valuable resource for consultants or other experts who may need to troubleshoot problems with your paint booth. The log can be a great resource for assessing any quality control issues in the finished product.
Tips for Paint Booth Filter Maintenance
Conducting paint booth filter maintenance is relatively simple.
When it is time to change your filters, you’ll need to turn off the paint booth and remove the old filters. You will then need to clean out the paint booth and install the new filters.
It is important to ensure that the new filters are correctly installed and sealed before turning the paint booth back on. It’s a good idea to have a second person check the seals and filter as well. Once complete, log the time, which employees conducted the maintenance, and any notes on the work in the log.
If you are having trouble changing your paint booth filters, are seeing increased quality issues or more frequent filter replacements, or if you are unsure of how often to change them, then we suggest consulting with an expert. This may be the sign of a more serious problem in your paint booth.
OTC has a team of experts who can help you troubleshoot problems with your paint booth and determine the best schedule for changing your filters.
Changing Paint Booth Filter Brands or Additional Work
It is important to consult with an expert before changing your paint booth filter style or brand. This is because different types of paint booths require different types of filters. If you use a low-quality filter in a high-volume paint booth, you could damage your paint booth. On the other hand, if you use an expensive filter when it isn’t necessary, you could be wasting money.
Efficient paint or spray booth operation requires a clear strategy with an eye on your goals.
OTC can help you set up a strategy and determine the best paint booth filter for your needs. We can also help you set up a regular maintenance schedule. Contact us today to learn more!
Stay up to date
SUBSCRIBE TO OUR BLOGPosts by Tag
- General Manufacturing (99)
- Compressed Air Solutions (54)
- Automotive (35)
- Finishing and Dispensing (31)
- Rotating Equipment (27)
- Industrial Automation (21)
- Maintenance & Repair Services (20)
- Case Studies (15)
- Electronics & Semiconductor (14)
- Sustainable Manufacturing (11)
- Energy Efficiency (10)
- Filtration (8)
- Energy, Power & Utilities (7)
- Food & Beverage (5)
- Oil & Gas (5)
- Pharmaceutical & Life Sciences (4)
- Industrial OEMs (3)
- Steel & Metal Manufacturing (3)
- Aerospace (2)
- Agriculture (2)
- Chemical & Petrochemical (1)
- Packaging & Processing (1)