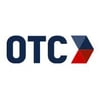
OTC Insights Team
Established in 1963, OTC Industrial Technologies (Ohio Transmission Corporation) is one of the largest industrial distributors & service providers in the United States. We're committed to seeing industrial operations advance through expert technical solutions & unmatched support using our years of experience.
The transmission in your car…
The lighting system for your smartphone camera…
The clock and brewing feature on your coffee maker…
The heating and cooling in your house…
Everywhere you look, automation is saving us time and money, making life better.
The same goes for manufacturing, where business leaders are under increasing pressure to reduce costs and increase production. Even as customer demands increase and the labor force shrinks, manufacturers are asked to do more. To stay a step ahead of the current challenges, manufacturers are relying on industrial automation systems.
What Are Industrial Automation Systems for Manufacturing?
An industrial automation system controls the processes and machinery used in manufacturing. These autonomous systems utilize software, robotics, sensors, controllers, and other technology to reduce the need for manual action or human input.
With industrial automation, machine and process control is handled by the system. Input arrives via sensors, and a preprogrammed action is taken by a controller unit. This is known as a closed loop system. In an open loop system, human input is needed for the process, but the actions are primarily completed by the system.
While not every manufacturing action can be handled by industrial automation, there are clear advantages when it can be used. Today, when companies are looking to reduce costs and increase production, an automated system that can run continuously, without the need for a shift change or lunch break, provides a benefit. Worker safety increases with automated systems, and the exacting action of an automated process eliminates the risk of human error and ensures consistency in product quality.
Examples of Industrial Automation Systems for Manufacturing
When looking at industrial automation systems for your plant or process, there are several technologies or systems that can be used to manage the tools. These include:
Programmable Logic Controllers (PLC)
A PLC uses a computer control system that has been preprogrammed to execute a process in manufacturing. Often, this is linked to sensor or other data collection tools. The PLC monitors the data for a trigger, which then starts the preprogrammed task.
Supervisory Control and Data Acquisition (SCADA)
A SCADA system monitors and collects data that can be used in the automation system. It uses sensors and other measuring tools to gather data. It is networked with other computers or digital systems that can use the data in manufacturing processes.
Industrial Robots
Robotics is an industrial tool that can mimic or perform an action in manufacturing, such as welding metal or applying paint. In addition, industrial robots can support humans by performing complex and difficult tasks. Some robotic systems can be simple, performing relatively repetitious jobs, while others can perform complex actions using intricate commands.
Human Machine Interface (HMI)
An HMI system links a human operator to the machine system. The operator controls the process equipment by initiating work and guiding the overall action. Typically, these systems also include a link to the SCADA system, translating the data into outputs that the operator uses in production.
Distributed Control Systems (DCS)
An automation system linking multiple nodes of automation and controller systems is known as a DCS. With it, you can automate multiple processes in production. The output of one node typically initiates the work on another node. Today, this has become a new generation in automation, with many systems using neural networks and artificial intelligence to manage and optimize work to further push what is possible in production.
Selecting an Industrial Automation System
With so many options available to manufacturers looking to automate production, it can be easy to get overwhelmed. There are strategies that can simplify implementation. Often, the implementation and setup of the system can be even more complex than the planning.
Before starting an industrial automation project or upgrade, it’s important to find a supplier and partner with the expertise and resources to make the project a success. This includes understanding the latest technology, how to utilize the technology to fulfill production goals, and how to use metrics to optimize the industrial automation system.
When you’re ready to take the next step in industrial automation, contact OTC Industrial Technologies to speak to one of our automation experts. Understand your options, have a plan, and reach your goals.
Stay up to date
SUBSCRIBE TO OUR BLOGPosts by Tag
- General Manufacturing (99)
- Compressed Air Solutions (54)
- Automotive (35)
- Finishing and Dispensing (31)
- Rotating Equipment (27)
- Industrial Automation (21)
- Maintenance & Repair Services (20)
- Case Studies (15)
- Electronics & Semiconductor (14)
- Sustainable Manufacturing (11)
- Energy Efficiency (10)
- Filtration (8)
- Energy, Power & Utilities (7)
- Food & Beverage (5)
- Oil & Gas (5)
- Pharmaceutical & Life Sciences (4)
- Industrial OEMs (3)
- Steel & Metal Manufacturing (3)
- Aerospace (2)
- Agriculture (2)
- Chemical & Petrochemical (1)
- Packaging & Processing (1)