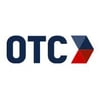
OTC Insights Team
Established in 1963, OTC Industrial Technologies (Ohio Transmission Corporation) is one of the largest industrial distributors & service providers in the United States. We're committed to seeing industrial operations advance through expert technical solutions & unmatched support using our years of experience.
Overview
A large equipment manufacturer purchased a complex, fully robotic finishing system for a new state-of-the-art production facility with the goals of optimizing productivity, reducing waste, and eliminating errors.
- Customer: Equipment Manufacturer
- Relationship with OTC: Nearly 2 Decades
Challenges
The manufacturer implemented a fully robotic finishing system in their advanced manufacturing facility to assist with their goals. However, while the system was highly efficient and successful in hitting these goals, the complex nature of the system required the team to keep a sufficient quantity of replacement parts on hand at all times to avoid production downtime.
The facility’s staff was tasked with predicting when spare parts would be necessary and determining how quickly inventory needed to be shipped to them.
Despite their best efforts, production downtime occurred, and shipping costs increased due to the need for rush order parts.
The manufacturer had to find a way to manage the finishing machine’s part inventory needs efficiently and cost-effectively to prevent production shutdowns, and rising expenses.
Solution
Faced with an inventory management challenge, the production facility turned to OTC Industrial Technologies for an effective solution.
First, the OTC team determined exactly what parts needed to be in stock to consistently keep the finishing system operating. By analyzing usage patterns and operational needs, they established minimum and maximum inventory levels tailored to the facility's requirements.
To streamline the parts ordering process, OTC implemented its Vendor Managed Inventory (VMI) system. This proactive solution includes regular visits to the facility—scheduled weekly, bi-weekly, or monthly—where OTC’s team:
- Counts the spare parts inventory to ensure accuracy.
- Provides a replenishment report recommending orders based on the predefined inventory thresholds.
This dual approach combines the automated tracking capabilities of the VMI system with manual monitoring, allowing OTC to anticipate future needs and ensure timely replenishment.
Additionally, the facility allocated a dedicated storage area to store the spare parts inventory and other essential equipment, ensuring easy access and better inventory control.
Results
OTC’s inventory management strategy and VMI system have been very successful in solving the manufacturer’s struggles to keep adequate quantities of spare parts in-house.
As a result of consistently maintaining proper inventory levels, the plant’s finishing machine has not been taken offline for parts shortages, optimizing productivity.
The facility’s staff now has more time to focus on their business, instead of managing equipment-related work stoppages. Due to the success of OTC’s inventory management solution, the manufacturer has begun to roll out this process to other facilities.
Learn more about how OTC’s inventory management process and VMI system can cost-effectively maximize your facility’s productivity and efficiency.
Stay up to date
SUBSCRIBE TO OUR BLOGPosts by Tag
- General Manufacturing (99)
- Compressed Air Solutions (54)
- Automotive (35)
- Finishing and Dispensing (31)
- Rotating Equipment (27)
- Industrial Automation (21)
- Maintenance & Repair Services (20)
- Case Studies (15)
- Electronics & Semiconductor (14)
- Sustainable Manufacturing (11)
- Energy Efficiency (10)
- Filtration (8)
- Energy, Power & Utilities (7)
- Food & Beverage (5)
- Oil & Gas (5)
- Pharmaceutical & Life Sciences (4)
- Industrial OEMs (3)
- Steel & Metal Manufacturing (3)
- Aerospace (2)
- Agriculture (2)
- Chemical & Petrochemical (1)
- Packaging & Processing (1)