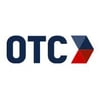
OTC Insights Team
Established in 1963, OTC Industrial Technologies (Ohio Transmission Corporation) is one of the largest industrial distributors & service providers in the United States. We're committed to seeing industrial operations advance through expert technical solutions & unmatched support using our years of experience.
Recent years have been a whirlwind of challenges and issues for manufacturers.
Empty store shelves, waiting lists for cars and electronics, and missing toilet paper have all left consumers wondering what was wrong with the industry. Semiconductor chip shortages have created bottlenecks that left distributors and downstream users fuming. A supply chain crisis and material shortages meant manufacturers were scrambling to stay a step ahead of disaster.
Now more than ever, manufacturers need to plan and reassess their current processes. You need to look to the future rather than rely on existing protocols. As the industry continues to overcome these challenges, you need to adapt. Staying ahead of the competition means looking ahead, planning and preparing.
That is the key to having a successful strategy for manufacturing automation.
Manufacturing Automation and Automated Manufacturing Tools in 2022
Here are the trends that we see having an impact on manufacturing automation in the coming year:
Adoption of Predictive Maintenance
Predictive maintenance has been standard strategy in manufacturing. In the past, employees would collect data from equipment, quickly review, and know when and what repairs would be necessary to prevent failure – they would just know the machine. It worked, but problems happened if an employee was out or a data collection was missed.
In recent years, with the development of sensor technology and the adoption of AI (artificial intelligence) and digital manufacturing, manufacturers have even more refined tools to implement predictive maintenance. With a SCADA (Supervisory Control and Data Acquisition) system, you can add automation to your predictive maintenance by collecting and analyzing data from your equipment.
Rather than replacing a knowledgeable employee, you can give them more control. You can turn that knowledge into a science, letting the employee focus on higher-priority tasks. As manufacturers continue to struggle with finding, hiring and retaining skilled employees, the need for SCADA systems, sensors and automation to support the employees you have on staff will be even more important in eliminating time-consuming manual processes.
The Rise of Reshoring
Between the supply chain crisis, raw material shortages and difficulties with shipping, downstream manufacturers need to find suppliers and OEMs that they can rely on. The result has been manufacturers bringing production processes back to the United States, or reshoring. Traditionally, many manufacturers moved operations out-of-country to capitalize on lower labor costs and a larger labor market to pull from. Overcoming these challenges to remain competitive on price will be critical for the companies that are reshoring.
One important tool for reducing production costs will be automation. Robotics, automation and sensor-driven machine intelligence will help these manufacturers keep labor costs low and enable the labor force in facilities to compensate for the increased demand. Look for manufacturers to continue to adopt robotics, automated manufacturing tools and sensor technology as production moves back to the Americas.
The Need to Boost Productivity
The continuing and increasing need for more skilled labor is a challenge that manufacturers face every day. Even as demand has increased, there are fewer available human resources and a smaller hiring pool. It’s a problem that’s expected to increase, with as many as 2.1 million manufacturing jobs that will be unfilled by 2030. To overcome this challenge, many manufacturers are turning to automation.
Automating processes will save time, reduce errors, and allow the skilled labor you have on hand to focus on higher priority work. In fact, it’s estimated that automation will increase overall productivity as much as 0.8 to 1.4% every year. With a full complement of sensors and automation processes in place, many production tasks can be completed faster and with minimal manual input. Automated tasks can be performed without need for breaks or shift changes. With automation supporting rather than replacing skilled labor by eliminating manual processes, companies can complete more work with the human resources they have available.
Continued Adoption of Digital Manufacturing
As manufacturers continue to embrace technology and systems like MES and PLM to improve productivity and efficiency, the need for accurate and timely data will increase.
Many manufacturers are eager to embrace digital and smart manufacturing. The technology has been available, but cost was prohibitive. This led to gaps in the technology adoption and continued reliance on manual processes. Today, that technology has become more affordable, and companies are implementing more digital manufacturing and smart factory tools and processes.
Look for this trend to continue as manufacturers embrace sensors and automated manufacturing tools as a critical component of advanced manufacturing strategies.
Embracing Sustainable Business Practices
This year, manufacturers are looking at environmental responsibility and sustainable processes as more than a trendy fad, but as a competitive strategy. With rising energy costs, the imminent risk of climate change and increased consumer demand for environmentally friendly products, manufacturers are rapidly embracing sustainable business practices.
This means taking a holistic view of the manufacturing process. Manufacturers are utilizing data to recognize where waste is being generated and identifying where there are opportunities for improvement. Sensors and automation are providing the data and process visibility necessary to make informed decisions and providing actionable intelligence needed for sustainability.
Look for companies to continue to rely on automation and data to empower sustainable business practices. With it, they can see where waste can be reduced and the negative impact on the environment minimized.
Looking Ahead to 2022 and Beyond
Even as we look to the future and the challenges ahead of us, there is a feeling of hope and excitement in the industry, much of it driven by the production insight and control offered by the latest automation and sensor tools. Many companies recognize that the dire circumstances that dominated manufacturing in recent times are receding. The market has shifted and there is opportunity ahead. From those challenges, we’ve all learned lessons that have made manufacturing stronger and more resilient.
Rather than fearing change, companies are embracing it to better production and their bottom line.
Stay up to date
SUBSCRIBE TO OUR BLOGPosts by Tag
- General Manufacturing (99)
- Compressed Air Solutions (54)
- Automotive (35)
- Finishing and Dispensing (31)
- Rotating Equipment (27)
- Industrial Automation (21)
- Maintenance & Repair Services (20)
- Case Studies (15)
- Electronics & Semiconductor (14)
- Sustainable Manufacturing (11)
- Energy Efficiency (10)
- Filtration (8)
- Energy, Power & Utilities (7)
- Food & Beverage (5)
- Oil & Gas (5)
- Pharmaceutical & Life Sciences (4)
- Industrial OEMs (3)
- Steel & Metal Manufacturing (3)
- Aerospace (2)
- Agriculture (2)
- Chemical & Petrochemical (1)
- Packaging & Processing (1)