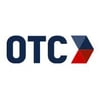
OTC Insights Team
Established in 1963, OTC Industrial Technologies (Ohio Transmission Corporation) is one of the largest industrial distributors & service providers in the United States. We're committed to seeing industrial operations advance through expert technical solutions & unmatched support using our years of experience.
Manufacturers need to look for opportunities for improvement. Shaving a few seconds off a production step, cutting energy use per unit, or reducing material needs can mean the difference between a profitable production run or losing money on every order.
For manufacturers looking to improve, there’s opportunity in exploring robotic systems and manufacturing automation.
The Function of Robots in Manufacturing
Robotic technology has had an impact on manufacturing for many years. Robotics takes the tasks required for traditional production and looks at available physical and digital technologies to complete them with higher efficiency, better results, or lower costs.
For manufacturers, the goal of robotics and automation is to boost production rates and profitability.
Optimizing the use of technology in production requires a plan. Not every task is suitable for robotics. Strategic use of robots means greater efficiency and more profits, while mistakes in the strategy can mean wasted resources.
The Advantages of Robots and Robotics in Manufacturing
Typically, robots (and autonomous robots especially) work best in high volume and highly repetitious production activities. The advantages of robots in production include:
Increased Productivity
Robots can work continuously, without the need for breaks or lunch. There are no lapses in concentration or coming in to work tired. They can work with precision that doesn’t suffer over time. If there’s no need to change over the robotic equipment for each order, this makes them highly productive.
Reduced Costs
After the initial investment in the system, there is typically a lower overhead cost for its use. With routine maintenance on the equipment, it should continue working as long as it is needed. Consistent, programmed work parameters mean lower scrap and fewer mistakes. With no need to rest, consistent work, and higher production, the return on that investment comes relatively quickly.
Higher Quality and Better Consistency
Working through automation and programming, rather than skill and practice, means consistent production work and no expensive errors. Accuracy and precision, requirements in high-quality work, are a strength of robotics. In addition, with a sensor system, the robotic automation can review the work to ensure it meets the production standards.
Increased Safety
Human workers will struggle to work in hazardous and dangerous conditions. Chemicals, heat, moving blades, and worse all present a danger for humans trying to complete production work. Intensive labor can also wear on a human worker, leading to safety issues. With the proper planning and preparation, a robot can handle those environments with ease, keeping human employees safe and eliminating unnecessary risk.
The Disadvantages of Robots and Robotics in Manufacturing
As beneficial as robots are to manufacturers, they can’t handle every task in the production cycle. They are better suited as a supplement rather than a replacement for traditional production methods. Understanding the disadvantages will help as you prepare your automation strategy.
Initial Costs and Investment
Adding a robotic or industrial automation system will require an upfront investment, and depending on the system, it may be significant. Before making that investment, you should work with an expert in robotics to ensure you are making a smart choice for your current needs. Look at the adaptability of the system to ensure it provides benefits even as your needs change.
Increased Need for Skilled Labor
Maintaining a robotic system requires skilled labor. Programming a robotic system for work requires specialized knowledge. Many times, a facility may not have these skills on staff. Look at partnering with a supplier with the services and experience on hand to supplement your existing workforce to maintain and optimize the robotic automation system.
Reassignment of Workers
The work done by the robotics is work that is no longer necessary for an employee to do. This may create friction with your staff. Rather than letting valuable workers go, look at retraining them or moving them to higher-priority tasks. Make sure to communicate your plan and work with the employees impacted by the new systems.
Process Limitations
Even as technology has progressed, and the capability and functionality of robots and automation have increased, there are still tasks not suitable for robotics. There are limits. Many companies that are in the process of implementing automation will find that the success of the new system is dependent on the other systems and processes around it. Look at using an end-to-end automation partner or integrator to provide a strategy that optimizes total production results, and not just processes related to the robotics.
Getting Started with Robots and Robotics for Manufacturers
Continual improvement is a hallmark of successful manufacturing. Robotics and automation represent a new phase in production methods, and now is the time for manufacturers to leverage the capabilities of technology to improve.
If you have questions about robotics or want to see how industrial automation can benefit you, then contact the team at OTC Industrial Technologies. Set up a no obligation meeting with one of our experts to explore your options. Call or contact us today.
Stay up to date
SUBSCRIBE TO OUR BLOGPosts by Tag
- General Manufacturing (99)
- Compressed Air Solutions (54)
- Automotive (35)
- Finishing and Dispensing (31)
- Rotating Equipment (27)
- Industrial Automation (21)
- Maintenance & Repair Services (20)
- Case Studies (15)
- Electronics & Semiconductor (14)
- Sustainable Manufacturing (11)
- Energy Efficiency (10)
- Filtration (8)
- Energy, Power & Utilities (7)
- Food & Beverage (5)
- Oil & Gas (5)
- Pharmaceutical & Life Sciences (4)
- Industrial OEMs (3)
- Steel & Metal Manufacturing (3)
- Aerospace (2)
- Agriculture (2)
- Chemical & Petrochemical (1)
- Packaging & Processing (1)