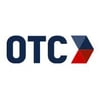
OTC Insights Team
Established in 1963, OTC Industrial Technologies (Ohio Transmission Corporation) is one of the largest industrial distributors & service providers in the United States. We're committed to seeing industrial operations advance through expert technical solutions & unmatched support using our years of experience.
Have you ever wondered what process takes a manufactured item from good to great?
The proper surface finishing process can make all the difference between a high-quality product and an unusable piece of material or scrap.What Is Finishing?
Finishing is the final step in the manufacturing process, establishing and determining the final surface elements of a material or product.
Surface finishing is the process by which the material or product is added to, altered, or reshaped to improve the ultimate quality and appearance of that item. Surface finishing acts as a protective coating and can improve an item's functionality and aesthetic. Moreover, it can be used across multiple mediums, such as metal, plastic, or wood. In automotive manufacturing, aerospace, furniture manufacturing, and many other industries, this can mean applying a paint finish and a sealant. A finish can also act as a protective coating for the product, with some finishes working primarily in that capacity.
Optimizing your surface finishing process can be achieved by implementing the right finishing system for your product or service.
What Is a Finishing System?
A finishing system or paint automation is a specialized production system that utilizes single- or multi-step processes to successfully resurface, shape, or alter material or product.
Many manufactured products require finishing before delivery to a customer or use. The final product determines the type of finishing process needed. Safety and industry-specific requirements are also considered.
Types of Finishing Systems
With so many finishes, there is a multitude of finishing systems to address the unique needs of your parts or service.
A metal finishing process may require various types of finishing to create a smooth, polished surface. For example, industrial finishing uses catalytic and electrolytic deposition to create a clear, strong outer coat for a final product. The type of finishing system used will be contingent on the desired results.
With technology and options on the market, manufacturers will need to pick and choose the finishing system that meets their customer requirements and production needs. A finishing system should streamline the final steps in the production process.
A Closer Look at Finishing Systems for Vehicle Manufacturing
Finishing is one of the most critical steps in automotive and other vehicle manufacturing. This process protects the final product, shielding it from outside elements, ensuring the longevity of the product, and ensuring a pleasing, higher-quality appearance.
Automotive finishing requires several steps to clean and paint the vehicle, then to cure the finish. The automotive parts move through the process stages in the finishing system. A typical automotive or vehicle finishing process might move through the following stages:
- Pretreatment: A cleaning process that removes loose particles, powder, or dust from the vehicle's surface.
- Electrodeposition: The vehicle body is dipped in an anti-corrosive paint to prevent future rusting. Following this process, the vehicle moves to a drying oven, where the paint hardens into a resilient film.
- Intermediate coating: This is the beginning of the painting process. Here, a robot paints the car to achieve maximum coverage and distribution. This is a critical step in the finishing process, and often uses robotics and automation to ensure a clean, high-quality, and error-free finish. Then, the vehicle moves to an oven for drying.
- Topcoating: The topcoat is the final portion of the painting process, which results in a hardened, shiny layer that maximizes the look and durability of the final product. The automobile is again placed in a drying oven to create a finished, optimal layer of protection.
What Are Custom Finishing Solutions?
While there are certainly variations between manufacturers and vehicles in this process, the core steps should be similar, as should the goal of the finish. This variation, and need for efficiency and cost savings where possible, is why many manufacturers rely on custom finishing solutions.
An expert in finishing can review the goal of the finished product, and the product itself. They can study the plant layout, the finishing chemicals, the required production times, and the available finishing tools and materials to identify possible efficiencies and cost savings in the process. They can engineer better finishing system options for manufacturers. This results in a custom finishing system.
Custom finishing systems can be designed around an assembly line, using robotics and manufacturing automation to move the product through each stage of the finishing process. For manufacturing services with a high production volume, creating a streamlined and efficient approach using robotics and automation to move items through each step of finishing can be essential for maximizing your output.
For operations with smaller, more refined finishing needs, you may need a finishing system that supports close attention to detail with more hands-on product availability and manual interaction. In this process, you may need more access to the product during finishing as well as an automation system for quality reviews.
Designing a Finishing Solution
Finishing solutions come in many shapes and sizes and should be designed around the specific needs of the manufacturer or business. Identify your needs and requirements, and evaluate your plant and current production processes. Once you’ve gathered information, assembled your requirements and understood your needs, reach out to an expert in finishing systems to discuss your options.
OTC offers a variety of finishing products that can help your operation meet your specific finishing needs. From spray guns to curing ovens, we can create a seamless process for a high-quality, lasting finish.
Contact OTC today to learn more about creating an efficient, cost-effective custom finishing solution.
Stay up to date
SUBSCRIBE TO OUR BLOGPosts by Tag
- General Manufacturing (99)
- Compressed Air Solutions (54)
- Automotive (35)
- Finishing and Dispensing (31)
- Rotating Equipment (27)
- Industrial Automation (21)
- Maintenance & Repair Services (20)
- Case Studies (15)
- Electronics & Semiconductor (14)
- Sustainable Manufacturing (11)
- Energy Efficiency (10)
- Filtration (8)
- Energy, Power & Utilities (7)
- Food & Beverage (5)
- Oil & Gas (5)
- Pharmaceutical & Life Sciences (4)
- Industrial OEMs (3)
- Steel & Metal Manufacturing (3)
- Aerospace (2)
- Agriculture (2)
- Chemical & Petrochemical (1)
- Packaging & Processing (1)