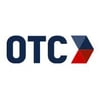
OTC Insights Team
Established in 1963, OTC Industrial Technologies (Ohio Transmission Corporation) is one of the largest industrial distributors & service providers in the United States. We're committed to seeing industrial operations advance through expert technical solutions & unmatched support using our years of experience.
Manufacturing is complex. A ballet of steel, people, tools, machines and activities.
Effective and efficient manufacturing requires alignment and synchronization of multiple moving processes. Are material shipments arriving on time? Is one step in production going to be completed in time for machining, or will you see downtime? Do you have enough workers to meet your production deadlines? Simply put, optimized production requires control and management of multiple resources across manufacturing channels.
The same alignment and synchronicity are necessary for your compressed air utility. As important as compressed air is to manufacturing, it’s an expensive and highly inefficient process. The process of preparing air for production — compressing it, cooling and drying the air, and transporting, regulating, and using it, often accounts for as much as 30% of a facility’s electric costs.
That inefficiency means there’s waste in compressed air utilities, and there are opportunities for improvement as well as reduced energy usage. An air evaluation can identify those opportunities and provide a rapid ROI and savings.
What Is an Air Evaluation?
With an air evaluation, an expert in compressed air will review both the supply side and the demand side of the compressed air utility at a facility.
The goal of the evaluation is to identify the requirements necessary for optimum performance. That means the compressed air system should run at the lowest pressure possible for manufacturing needs. On the supply side, the compressed air should be produced and stored at the highest necessary pressure.
For industrial air compressors and manufacturers, this means the air evaluation must evaluate the entire system. Both the demand side and the supply side are connected, and optimization means addressing both sides of the equation.
The Requirements of a Successful Air Evaluation
To get the best possible visibility into regular operations, a successful evaluation will be conducted during normal production cycles. The evaluation should cover the priorities and problems facing the production team. What are the critical needs for successful operations, and where are the issues and challenges? Data must be collected and analyzed at multiple points in the compressed air process. It is critical that the evaluation be conducted over time rather than with a single snapshot. It needs to account for both the high and low points of usage.
The entire system needs a comprehensive review to account for and identify every factor that could be impacting your compressed air utility, from the air intake and filtration to the point in production where it is used. Problems that will be identified in the analysis could include:
- Leaks and poor piping
- Rust and old or poorly maintained equipment
- Poor or inadequate piping
- Pressure at multiple points in the system
- Equipment misuse
An evaluation doesn’t just cover the problems but also typical use and how the entire system can be optimized and improved. The team will be looking at several items that can impact compressed air usage. These include:
- Demand requirements
- Critical pressure applications
- System capacity
- The piping system requirements and flow
- The energy storage system
- The maintenance strategy as it relates to demand requirements
- Future requirements
- Best practices for the system
When finished, the evaluation team should have as complete a view as possible of your air compressor usage. From that, they can make informed decisions on improvement.
The Benefits of a Compressed Air Evaluation for Manufacturers
For many manufacturers, compressed air is simply a utility, and it either works or doesn’t. But, as with any complex system, there are a number of factors in a compressed air system that can increase costs, reduce efficiency, decrease production safety, and slow cycle times. These could include:
- Excessive pressure
- Leaks
- Pressure that is too high or too low
- Missing system components such as air curtains or nozzles
- Inadequately designed or implemented equipment
- Poorly applied filters, connectors, regulators, or dryers
- Bad piping
- Misaligned air receivers
- The wrong, or poorly selected, air supply equipment
When complete, the evaluation will typically return a series of steps that, if followed, will reduce energy usage and costs by as much as 25 to 50 percent and deliver a return in a few months.
Additionally, the evaluation will likely include additional suggestions that will offer further benefits or savings. For example, replacing machines or equipment, modifying processes, updating best practices, or even working with a managed services provider who can deliver and manage the utility.
Conducting an Air Evaluation for Your Facility
An air evaluation is not something that should be conducted internally. An outside expert in air systems and compressed air, one who can look objectively at your current processes, will provide a more effective analysis. They not only bring expertise that internal resources may not have, but they also have a wealth of best practices and insight developed from experience with past evaluations.
That insight and experience will benefit your compressed air system and overall operations. By focusing on the issues facing production and the expense of an air compression utility, in most cases, manufacturers will see a rapid ROI for the air evaluations and subsequent recommended steps.
If you have questions, or want to schedule your own air supply evaluation, then contact the compressed air team at OTC Industrial Technologies. We have decades of collected experience and have saved manufacturers millions in reduced energy usage and more efficient operations.
Stay up to date
SUBSCRIBE TO OUR BLOGPosts by Tag
- General Manufacturing (99)
- Compressed Air Solutions (54)
- Automotive (35)
- Finishing and Dispensing (31)
- Rotating Equipment (27)
- Industrial Automation (21)
- Maintenance & Repair Services (20)
- Case Studies (15)
- Electronics & Semiconductor (14)
- Sustainable Manufacturing (11)
- Energy Efficiency (10)
- Filtration (8)
- Energy, Power & Utilities (7)
- Food & Beverage (5)
- Oil & Gas (5)
- Pharmaceutical & Life Sciences (4)
- Industrial OEMs (3)
- Steel & Metal Manufacturing (3)
- Aerospace (2)
- Agriculture (2)
- Chemical & Petrochemical (1)
- Packaging & Processing (1)