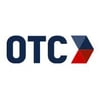
OTC Insights Team
Established in 1963, OTC Industrial Technologies (Ohio Transmission Corporation) is one of the largest industrial distributors & service providers in the United States. We're committed to seeing industrial operations advance through expert technical solutions & unmatched support using our years of experience.
There are a multitude of uses for an air compressor in manufacturing and industrial applications. Often, an emergency can lead to an immediate need for a rental air compressor. However, without a little preparation work, you may be throwing money away on that rental unit.
For many manufacturers, air compressor downtime can mean a production shutdown. Rental air compressors offer a quick solution to downtime or provide additional capacity when needed.
What You Need to Know Before Renting an Air Compressor
Many tools are powered by compressed air. Abrasive blast equipment, a staple in finishing and material preparation, can smooth a rough surface and remove contaminants, shape material, even roughen a surface for further treatment. Air compressors are critical for paint sprayers and refrigerants. Gases used in manufacturing are propelled by compressors.
Here are a few questions you should ask before renting an air compressor.
- How long will the downtime be?
Often, a rental unit is a quick and convenient fix for a problem. Repair work on your air compressor can mean downtime, but a rental unit can keep production flowing during maintenance.
However, if your costs for a rental unit are higher than expected or if the cost of transporting and installing rental units isn’t included in the cost analysis, then it may be worthwhile purchasing a new air compressor as a backup, or considering alternative options. Especially for companies struggling with an older or inadequate air compressor, the cost of emergency rentals may be higher than purchasing or leasing a new, more efficient unit.
- Is the cost of renting an air compressor higher than the expected return on the work?
For many companies, the expenses for renting an air compressor can be included in the work or order estimate. If that cost isn’t included, then the rental can significantly diminish the return. Also consider the additional costs that may be involved in the rental, including renting a unit from a company that isn’t an expert in air compressors and getting a unit that is more expensive than your needs. These hidden costs can be very painful.
In these cases, it may be worthwhile to look at purchasing a unit, even if it doesn’t see continual use. Over time, the capital expense will be covered by additional work. Finding a more reliable, long-term partner with expertise in air compressors can help you in matching your needs and requirements with the right rental, helping eliminate those hidden costs.
- Do I have the internal resources and expertise to maintain the air compressor?
Many companies will rely on a rental air compressor because they don’t have the knowledge or expertise necessary to maintain and optimize the purchase of a unit. By letting the rental company handle the installation, maintenance, and labor for the air compressor, they aren’t putting pressure on their already overworked skilled labor. Employees can focus on higher priority tasks, providing a quick and easy solution.
Other times, when you have the expertise on staff, you’ll see greater savings from handling the maintenance work on the air compressor by yourself. The purchased unit can be paid off as a capital expense, reducing costs over time.
Renting versus Buying an Air Compressor
Before renting an air compressor for any significant time, conduct a cost analysis to see if it’s better to purchase a new or replacement unit. Look at whether it’s possible to adjust the production schedule to reduce downtime during maintenance. Look at not only the cost of an individual rental, but the lifetime cost of renting an air compressor against the lifetime cost of purchasing a new air compressor.
By answering the questions above, and reviewing the results of the cost analysis, you can make an informed decision about your air compressor needs.
Keep in mind, however, that renting and purchasing an air compressor aren’t your only options for solving your compressed air needs.
The Benefits of DIRECTAIR® Service for ESG and Energy Savings
DIRECTAIR® from OTC Industrial Technologies is a total solution for compressed air, providing it as a utility rather than simply leasing or renting a compressed air unit.
You have the benefit of clean, reliable compressed air without the worry or risk of renting or owning the air compressor. Since DIRECTAIR® is managed by experts in compressed air, you’ll often see energy savings supporting ESG (Environmental, Social, and Governance) goals for the company. With advanced monitoring, and regular maintenance and performance evaluations by the compressed air experts at OTC, you have optimal performance for the system at a set cost that you can budget for.
With DIRECTAIR®, you have all the benefits of clean compressed air without the risks and additional costs that often come from long-term rental.
If you’d like to talk to OTC about your compressed air needs, whether it’s a rental unit, purchasing a new system, or evaluating the benefits of the DIRECTAIR® program, then contact OTC today. Set up an appointment and explore your options.
Stay up to date
SUBSCRIBE TO OUR BLOGPosts by Tag
- General Manufacturing (99)
- Compressed Air Solutions (54)
- Automotive (35)
- Finishing and Dispensing (31)
- Rotating Equipment (27)
- Industrial Automation (21)
- Maintenance & Repair Services (20)
- Case Studies (15)
- Electronics & Semiconductor (14)
- Sustainable Manufacturing (11)
- Energy Efficiency (10)
- Filtration (8)
- Energy, Power & Utilities (7)
- Food & Beverage (5)
- Oil & Gas (5)
- Pharmaceutical & Life Sciences (4)
- Industrial OEMs (3)
- Steel & Metal Manufacturing (3)
- Aerospace (2)
- Agriculture (2)
- Chemical & Petrochemical (1)
- Packaging & Processing (1)