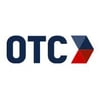
OTC Insights Team
Established in 1963, OTC Industrial Technologies (Ohio Transmission Corporation) is one of the largest industrial distributors & service providers in the United States. We're committed to seeing industrial operations advance through expert technical solutions & unmatched support using our years of experience.
If your operation doesn’t rely on data-driven decision-making, it’s time to start.
Using data to identify and address problems is one of the easiest and most effective ways to improve overall efficiency. At OTC Industrial Technologies, we understand how to collect data on your most essential metrics and use this data to refine your business and improve your bottom line.
The Importance of Using Data in Manufacturing
Without the right data, you’re relying only on guesswork and luck to optimize and manage production. Traditional information resources like employee reports, shipping records, and production data recorded by hand can give you valuable insights, but they aren’t as accurate or reliable as hard data.
Information collected directly from the machines in your operation not only provides you with a more robust set of data but also comes with the benefits of automation that eliminate mistakes in production records and data collection. Automatic data analysis and visualization keep your finger on the pulse of your business and help identify problems before they can do damage.
How to Get Started Using Data
Automated data collection and analysis aren’t as complex or difficult to implement as many manufacturers believe. Understanding how manufacturers use data to increase efficiency can help you identify early goals. Here are five ways that manufacturers can use data:
1. Collect Data Directly from Your Machines
Before you can start visualizing and analyzing information, you must ensure that your data comes from the right source. Employees manually reporting data can be helpful, but human error means that these reports will never be as accurate as reports generated automatically by your equipment. Start by identifying the data that you need, and what machines have data collection systems built in. For example, if a machine needs frequent repair, then see if you can track temperature or run speed to identify when maintenance could prevent a shutdown. Or, if you want to increase OEE (Overall Equipment Effectiveness) then look at tracking when machines are operating. If you have questions on what data you can collect, how it can be collected, or how to make the most of your production information, then contact OTC for help.
2. Use Dashboards to Visualize Data
It’s hard to see areas of potential improvement in raw data. Dashboards and other data visualization tools allow you and your team to see trends and patterns quickly. Visualizing data helps you find areas of waste and opportunities for improvement. For example, with a dashboard that tracks trends, you can easily identify issues that will have a negative impact on quality, such as equipment heat or power draw.
3. Set Thresholds for Automatic Alerts
Don’t wait for your equipment to break before scheduling repairs. Setting up automatic alerts gives you time to address issues before they stop production. You can use these alerts to track when your machines need maintenance or operate at unsafe levels. For example, set a threshold for maximum and optimal heat on equipment. When the maximum temperature is reached, the machine can be set to shut down automatically, and a notification sent to the maintenance crew. Automatic notifications keep you one step ahead of critical breakdowns and stoppages.
4. Identify Areas of Waste
Data can be used to identify areas of waste in your processes, which will increase the efficiency of your operation. When analyzing your data, measure your operation’s energy and resource consumption against the output. If any machines are drawing more energy than they need to operate reliably, you can test different settings to find ways to reduce your energy bill. That can also be a sign that the equipment needs maintenance or repair. Additionally, you can use data to identify overproduction and waste. If a machine is running faster or more than is needed, you can scale back operations to save energy.
5. Identify your ROI
Collecting, visualizing, and assessing your data are all essential to increasing the efficiency of your operation, but these steps are meaningless if they don’t produce results. As you implement production changes using the data, measure and track the results. For example, if you reduce equipment usage during slower production times to reduce energy waste, then you should start tracking the cost of energy over time. The data should provide you with an ROI for the data and analytics efforts. Over time, this data and savings will help pay for additional data projects.
Are You Ready For the Data?
Want to get started with implementing a data and analysis project? The experts at OTC can help. Our team is standing by to answer any questions you have and to provide recommendations on increasing the efficiency of your manufacturing business. Don’t wait to get the help you need. Contact OTC to start leveraging your data.
Stay up to date
SUBSCRIBE TO OUR BLOGPosts by Tag
- General Manufacturing (99)
- Compressed Air Solutions (54)
- Automotive (35)
- Finishing and Dispensing (31)
- Rotating Equipment (27)
- Industrial Automation (21)
- Maintenance & Repair Services (20)
- Case Studies (15)
- Electronics & Semiconductor (14)
- Sustainable Manufacturing (11)
- Energy Efficiency (10)
- Filtration (8)
- Energy, Power & Utilities (7)
- Food & Beverage (5)
- Oil & Gas (5)
- Pharmaceutical & Life Sciences (4)
- Industrial OEMs (3)
- Steel & Metal Manufacturing (3)
- Aerospace (2)
- Agriculture (2)
- Chemical & Petrochemical (1)
- Packaging & Processing (1)