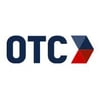
OTC Insights Team
Established in 1963, OTC Industrial Technologies (Ohio Transmission Corporation) is one of the largest industrial distributors & service providers in the United States. We're committed to seeing industrial operations advance through expert technical solutions & unmatched support using our years of experience.
It seems like everywhere you turn, there is a sign that reads, “now hiring.”
Yes, the shortage of skilled workers is alarming, and unfortunately, the manufacturing industry isn’t exempt. A lack of skilled workers or labor can mean limited production capacity for manufacturers. It can mean turning down profitable work or relying on unskilled and inexperienced workers. It can lead to unsafe working conditions and lost customers.
Develop a Manufacturing Talent Strategy
Fortunately, there are a few things manufacturers can do to attract top-notch talent, although it may require rethinking their traditional way of doing things.
Improve Work Conditions
A recent survey indicated that the number one reason employees left their places of employment during the great resignation was due to low pay and toxic work conditions. By creating a positive work environment that aligns with people’s values and offers opportunities for growth along with reasonable compensation, manufacturers will be in a better position to attract new talent.
Leverage On-Demand Labor
Rather than hiring for temporary spikes in workload or overextending their existing workforce, manufacturers can turn to on-demand labor. Companies that offer on-demand manufacturing or logistics labor act as a partner, connecting the manufacturer to skilled, high-quality workers through a convenient marketplace. This partnership offers operational efficiency and resources for continuous improvement. It's a flexible workforce and labor solution for employees and employers. Businesses have a fast response to spikes in demand with low costs to scale, while employees have increased opportunities and can develop their skills while exploring new opportunities.
Utilize Work Study Opportunities
If creating your own manufacturing work-study program isn’t an option, consider partnering with a local college or university that offers manufacturing work-study programs. These work-study programs will attract students looking for real-life experience and who have some of the basic skills required for the position. Consider offering a scholarship or internship to evaluate and support new workers in the industry.
Partner with a Service Provider
Sometimes you may not need to hire expensive skilled labor. Instead, sign a long-term contract with a service provider. This will give you a larger pool of expertise and workers at a potentially lower cost. Some areas where you can utilize a service provider include:
- Automation services: Rather than purchasing an automation system and using an internal resource to design and implement, use an end-to-end, turnkey automation solution provider. They can help with the design to meet your manufacturing goals, install it and provide training. If maintenance and repair are a concern, include those services in the contract.
- Repair services: Any equipment will have its share of wear and tear, and maintenance and repair teams are often the first to see loss when skilled labor becomes an issue. Use a service provider for larger or more complex repair work. Many providers offer on-site and field service work and convenient fabrication and repair shops to handle the most demanding repairs and equipment modifications.
- Preventative maintenance: While you may first use an outside service for repair, you can also use them for standard maintenance. This reduces problems due to equipment malfunctions and breakdowns, and regularly scheduled, proactive maintenance is a low-cost way to keep equipment running efficiently without labor costs.
- Training: Rather than hiring, an outside service provider may also offer training to give your existing team the necessary skills. This will allow you to use your current employees well, help them implement best practices for future jobs, and provide additional job value to employees. As a result, your manufacturing business will be spared the expense and hassle of hiring additional labor or using outside contractors.
Mitigating the Skilled Labor Crisis
The manufacturing industry has recognized a skilled labor gap for years, but minimal effort has been taken to solve or mitigate it. It’s come down to the factories and jobsites to find their own solutions.
You aren’t in this alone. If you have questions or need help, contact the team at OTC Industrial Technologies. We work with manufacturers across the country and have an experienced team of engineers and experts available to provide you with the help you need.
Stay up to date
SUBSCRIBE TO OUR BLOGPosts by Tag
- General Manufacturing (99)
- Compressed Air Solutions (54)
- Automotive (35)
- Finishing and Dispensing (31)
- Rotating Equipment (27)
- Industrial Automation (21)
- Maintenance & Repair Services (20)
- Case Studies (15)
- Electronics & Semiconductor (14)
- Sustainable Manufacturing (11)
- Energy Efficiency (10)
- Filtration (8)
- Energy, Power & Utilities (7)
- Food & Beverage (5)
- Oil & Gas (5)
- Pharmaceutical & Life Sciences (4)
- Industrial OEMs (3)
- Steel & Metal Manufacturing (3)
- Aerospace (2)
- Agriculture (2)
- Chemical & Petrochemical (1)
- Packaging & Processing (1)