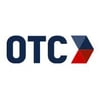
OTC Insights Team
Established in 1963, OTC Industrial Technologies (Ohio Transmission Corporation) is one of the largest industrial distributors & service providers in the United States. We're committed to seeing industrial operations advance through expert technical solutions & unmatched support using our years of experience.
Want to boost production and production efficiency? Looking to increase manufacturing output and save costs? The answer may already be on your shop floor.
No matter how much you initially spend on a pump or how much care you take in maintaining it, it will wear out, and you will need a new pump. However, implementing more rigorous preventative maintenance and using outside expert services for consultation and repair for your pumps can deliver production efficiency and business benefits beyond a longer lifespan for your pump. Benefits that may surprise you.
Take Control with Pump Repair Services
In the past, many companies were reluctant to use outside resources like a supplier for repair and maintenance. They would use equipment like a pump until it broke. If the internal team couldn’t fix it, or the repair wasn’t simple enough, it was easy to purchase and install a new pump.
Today, due to rising costs, low equipment inventory, and supply chain issues for parts, purchasing a new pump isn’t so simple. Manufacturers need to adjust their thinking about service and repair for pumps to accommodate current market conditions. That includes looking at more extensive repair services and investing more resources in pump and motor maintenance.
In addition to increasing the life of your current equipment, there are other benefits to repair services for manufacturing pumps.
Preventative Maintenance Saves Money
Many manufacturers don’t have a preventative maintenance plan in place. In the past, with easy access to new pumps or replacement parts, there was little reason to waste time and effort on preventative maintenance. Today, with increasing costs for parts and equipment, and lead times for new equipment that can be months or even years, preventative work is critical. Regular checks and rigorous testing can prevent problems and save money in the long run.
Avoid Downtime to Increase Production
Today, spare parts for a pump may not be available, or a critical part may be on backorder with a long lead time. That can lead to downtime for the pump or inefficient workarounds for the damaged unit. Workarounds often lead to decreased production. Repair or service work on the pump can eliminate or significantly reduce downtime. You get more products out the door.
Increase Efficiency and Boost Output
A repaired and well-maintained pump works efficiently. A pump that isn’t in optimal working order will have a reduced flow rate or other problems. You won’t see the expected pump volume. It isn’t as efficient. That can reduce your output and cause problems further downstream in your production processes. When a problem with a pump is discovered, many companies will find that other work processes have been adjusted to compensate.
Improve Equipment Reliability and Safety
A problem with a pump that isn’t discovered or is left malfunctioning can have a cascading effect on your overall production reliability. Constant “quick” repairs to keep the pump working make it hard to schedule and plan work or reliably forecast output. It can also be a safety issue, as the employees working near the pump or handling the repairs face increased hazards.
Avoid Supply Chain Challenges
As we mentioned earlier, supply chain issues are expected to continue for the foreseeable future. While these issues will affect all of us, there are proactive steps you can take to prevent internal supply chain problems. These steps include setting up regular maintenance and utilizing expert repair services. During these difficult times, if you can keep your pumps in good working condition, you won’t need to order a new pump, wait for the delayed delivery, or settle on an available pump that may not precisely meet your needs.
Training for Your Internal Team
Many suppliers that offer repair and maintenance services are willing to provide a review of the work done with your internal maintenance team. They can help you build better best practices around your internal repair and maintenance programs. Think of it like invaluable on-the-job training for your team. Over time, the added benefit of this training and practice will increase the skill and expertise of your employees, boosting the ROI you see from the services.
Implementing Proactive Maintenance
As a manufacturer, you likely already have a maintenance plan in place. You’ve researched pump repair services in the past. None of the information we’ve presented here may come as a surprise.
However, with the current challenges facing manufacturers and the opportunities waiting for companies that can reliably meet market demands, now is the time to double down on repair. Have a pump expert at OTC visit your facility to review the pumps you have on hand. See if there are any opportunities for additional preventative maintenance. Look at increasing efficiency with on-site adjustments. Order critical replacement parts now rather than after a problem happens.
Those steps may not have delivered an ROI in the past, but in the current market, they can be invaluable. Even preventing one problem can deliver a significant boost to your revenue.
If you have questions or want a free consultation with someone on our pumps and motor team, then contact us today. Don’t wait until your pump stops and production is down. Schedule time now with OTC to discuss your needs and the challenges you’re facing.
Stay up to date
SUBSCRIBE TO OUR BLOGPosts by Tag
- General Manufacturing (99)
- Compressed Air Solutions (54)
- Automotive (35)
- Finishing and Dispensing (31)
- Rotating Equipment (27)
- Industrial Automation (21)
- Maintenance & Repair Services (20)
- Case Studies (15)
- Electronics & Semiconductor (14)
- Sustainable Manufacturing (11)
- Energy Efficiency (10)
- Filtration (8)
- Energy, Power & Utilities (7)
- Food & Beverage (5)
- Oil & Gas (5)
- Pharmaceutical & Life Sciences (4)
- Industrial OEMs (3)
- Steel & Metal Manufacturing (3)
- Aerospace (2)
- Agriculture (2)
- Chemical & Petrochemical (1)
- Packaging & Processing (1)