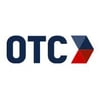
OTC Insights Team
Established in 1963, OTC Industrial Technologies (Ohio Transmission Corporation) is one of the largest industrial distributors & service providers in the United States. We're committed to seeing industrial operations advance through expert technical solutions & unmatched support using our years of experience.
The supply chain crisis has had an unprecedented impact on manufacturers and consumers worldwide. We’re all feeling it, from the empty store shelves and the higher cost of goods, to the challenges facing businesses including long wait periods for replacement parts, or an endless back order list for the delivery of new equipment.
These issues can lead to paying more for replacement parts or systems, which means you cut your profits or pass along the higher costs to customers. Without a solution, it can lead to a halt in production altogether.
How to Mitigate the Supply Chain Crisis for Finishing Departments
OTC understands the struggle. Here are nine ways your company can overcome the supply chain crisis and keep production moving in your finishing department.
1. Increase Finishing Maintenance Protocols
Paint booth maintenance means keeping your booth clean, effective, compliant, and safe. Regularly maintaining your paint systems will decrease the number of issues that could come up in the future.
Furthermore, proper maintenance will ensure the system is safer and more successful. It will also save your company money since the better the system is cared for, the longer it will last. You will often see an increase in quality along with fewer issues or breakdowns.
Many businesses are struggling with worker shortages. There are solutions if your company is short staffed, with no one available for maintenance work. Consider turning to an outside resource to manage maintenance. Many times, experts in finishing systems can provide a higher level of maintenance, and help you identify components or parts that may need to be replaced. They can also make recommendations to update or improve efficiency for your booth.
2. Install Monitoring Systems
A monitoring system is software and sensors that automatically collect and analyze machine and environmental data. They help monitor their infrastructure, providing eyes that are constantly evaluating production for problems. Alerts inform the right workers in the event of malfunctions and disruptions.
Monitoring systems can prevent some repair costs by alerting when maintenance is needed. They can reduce downtime or the need for extensive repairs. If you are interested, talked to an OTC representative about what you can do to prevent work stoppage and equipment failure before it happens.
3. Rely on Finishing System Repairs
In this age of back orders, look at repairing equipment when possible, instead of buying new. Making repairs to tools such as paint spray guns can be quick and easy, and will keep production rolling. For larger or more complex products, like finishing systems or smart paint systems, OTC experts can assist you with evaluating your repair and replacement options.
4. Stock up on Inventory
In a supply chain crisis, it’s better to buy when available than do without in the future. Make sure to have backup inventory. While overstocking is typically a bad business practice, keeping a few reserve items or tools can prevent delays and disruptions in business.
OTC is one of the largest industrial distributors and service providers in the United States. We offer one of the broadest ranges of quality equipment and systems with the support of our vendors. Consult with OTC to discuss your production needs and let our team help you create an inventory plan.
5. Prioritize Your On-Hand Inventory
During a material shortage or a supply chain disruption, certain products will be a higher priority. When stocking up on inventory, do research and categorize items according to highest priority. Your goal should be to keep production moving and avoid shutdowns.
6. Evaluate Alternative Equipment When Possible
In these difficult times, make sure to rely on expertise. While one item you need might not be available, an alternative part, piece of equipment, or machine might work just as well. It may not have been your first choice, but it should keep production moving with minimal disruption. Talk to your supplier or distributor partner about your options.
7. Communicate with Customers
When your company learns of any potential shortage in inventory, delay in production, or shutdown, make sure to notify your customers immediately. Give them as much information as possible and suggest any available alternatives or a timeline for when you will be able to fill orders again. It might be a difficult conversation, but in the long run it is the best option. We’re all dealing with inventory delays, and they should understand.
8. Research Alternative Logistics
Truck driver strikes and shortages are among the things that have caused a significant backlog in logistics. If this is at the root of the delay, consider alternative shipping options to meet any change in deadline and customer demand. Using a different supplier with access to more shipping options may help mitigate these problems.
9. Rely on Fulfillment Partners
While you are an expert in manufacturing, you may not be a supply chain, logistics, or purchasing expert. Make sure to rely on your distributors. Their fulfillment experts are equipped to handle all potential disruptions in the supply chain and should have options available for you.
OTC Industrial Technologies’ Expertise is Available
OTC Industrial Technologies is here to help you grow your business with premier product lines, innovative solutions, and unparalleled technical expertise. We understand finishing and can bring insight and experience to your challenges that you may not find elsewhere. That includes overcoming supply chain challenges to keep your business moving. Reach out to one of our experts today to learn more.
Stay up to date
SUBSCRIBE TO OUR BLOGPosts by Tag
- General Manufacturing (99)
- Compressed Air Solutions (54)
- Automotive (35)
- Finishing and Dispensing (31)
- Rotating Equipment (27)
- Industrial Automation (21)
- Maintenance & Repair Services (20)
- Case Studies (15)
- Electronics & Semiconductor (14)
- Sustainable Manufacturing (11)
- Energy Efficiency (10)
- Filtration (8)
- Energy, Power & Utilities (7)
- Food & Beverage (5)
- Oil & Gas (5)
- Pharmaceutical & Life Sciences (4)
- Industrial OEMs (3)
- Steel & Metal Manufacturing (3)
- Aerospace (2)
- Agriculture (2)
- Chemical & Petrochemical (1)
- Packaging & Processing (1)