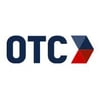
OTC Insights Team
Established in 1963, OTC Industrial Technologies (Ohio Transmission Corporation) is one of the largest industrial distributors & service providers in the United States. We're committed to seeing industrial operations advance through expert technical solutions & unmatched support using our years of experience.
Setting a manufacturing budget, or even balancing one in the face of demanding deadlines and the speed of modern production, can feel like throwing darts blindfolded.
Can you trust last year’s budget or results? Have you accounted for enough indirect costs, or maybe you’ve overbudgeted too much? Is there anything more you can do to reduce production budgets and boost profits? Is your overhead bloated? Are you preparing for the future and putting enough into facility improvements? What about your competition — have you done enough to protect your business from them?
It can feel like you need a crystal ball and a fortune teller assistant to successfully manage your budget, especially if you’re also managing constantly changing, fast-moving production activities. With getting product out the door, finding solutions for issues on the floor, adjusting to the shifting demands of modern manufacturing, and staying a step ahead of problems, constantly struggling with a budget can hold you back.
Managing Your Budget with Flexible Rental Air Compressor Options
As a manufacturing leader, you need options when it comes to balancing your budget against the demands of fast-paced manufacturing. Rental solutions can help.
When a system or machine breaks down and money hasn’t been budgeted for a replacement, a rental unit can ensure your team has the equipment or service they need until the next budget cycle. You can avoid a costly budget overrun while minimizing disruption to production.
Rental systems can also work as a cost avoidance measure. When if an air compressor requires repairs or can’t adequately cover new production demands, then a rental unit can be used to fill in the gap. Rather than putting additional strain on your infrastructure, strain which can cause a breakdown, or allowing inefficiencies to slow production, you can meet demand with a rental air compressor.
The key is recognizing a need and addressing it with available resources, rather than letting an issue become an even bigger problem by ignoring it.
Taking Advantage of Rental Air Compressors
Let’s review a few situations where a rental unit can help mitigate budget problems:
Increased Production Needs
What happens if a large order comes in and suddenly the plant needs more compressor capacity? Purchasing a new or additional air compressor might not be feasible. Trying to utilize existing air capacity can cause energy costs to skyrocket and lead to significantly higher maintenance costs due to the strain on the system. While conducting an air audit is critical, a rental unit can cover the gap at a much lower overall cost before the air audit while ensuring the production team has the reliability and service they need.
Production Rollbacks
Similarly, if there’s a rollback or reduction in production needs, you can rent chillers or compressors that can better suit current demands rather than using equipment that isn’t applicable. This will reduce your overall energy costs, so the rental quickly pays for itself. In addition, the rental unit will allow you to evaluate compressor capacity before you need to purchase a new unit designed to meet current demand.
Equipment Failure
When an air compressor goes down and a costly repair or a new compressor isn’t in the budget, a temporary air compressor can cover the gap until you’ve budgeted for a permanent solution. Similarly, if you have a damaged compressor, rather than trying to eke out a little more use by delaying a high-cost repair, turn to a rental. Using the rental keeps production moving until you have a repair or replacement unit online.
Proof of Concept
Before setting aside a budget or purchasing a new air compressor, evaluate your options with a rental unit. See if a new compressor, an additional chiller, an oil-free option, or a new control system can deliver the capacity or functionality you need to make the investment worthwhile.
Cover Capacity for Equipment on Back Order
Due to supply chain issues and demand, some new air compressors are more than a year out from shipping. The manufacturers waiting on this equipment, expecting that compressed air capacity, are left in a bind. A rental unit can fill in that gap and ensure the manufacturer has reliable, clean air until the new unit is in place.
Evaluating Your Budget Options for Compressed Air
Not every rental supplier is created equal.
Before selecting a supplier for rental equipment, discuss your potential budget with them to see if they have options that may better meet your needs.
Critical Rental Solutions has experience working with manufacturers of all sizes and in many verticals. They can approach the budget issues and payment options for the rental equipment from multiple angles. Rental equipment, even long-term air compressors or cooling unit rentals, aren’t a capital expenditure, so they won’t impact the budget in the same way as a new unit.
Take the stress out of managing both production and your budget by Critical Rental Solutions today. Discuss your production needs and work with them to deliver a solution that works best for you.
Stay up to date
SUBSCRIBE TO OUR BLOGPosts by Tag
- General Manufacturing (99)
- Compressed Air Solutions (54)
- Automotive (35)
- Finishing and Dispensing (31)
- Rotating Equipment (27)
- Industrial Automation (21)
- Maintenance & Repair Services (20)
- Case Studies (15)
- Electronics & Semiconductor (14)
- Sustainable Manufacturing (11)
- Energy Efficiency (10)
- Filtration (8)
- Energy, Power & Utilities (7)
- Food & Beverage (5)
- Oil & Gas (5)
- Pharmaceutical & Life Sciences (4)
- Industrial OEMs (3)
- Steel & Metal Manufacturing (3)
- Aerospace (2)
- Agriculture (2)
- Chemical & Petrochemical (1)
- Packaging & Processing (1)