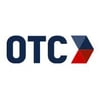
OTC Insights Team
Established in 1963, OTC Industrial Technologies (Ohio Transmission Corporation) is one of the largest industrial distributors & service providers in the United States. We're committed to seeing industrial operations advance through expert technical solutions & unmatched support using our years of experience.
For any manufacturer with a growing, scaling business, plant floor space can quickly become an issue that can bite deep into productivity.
Adding a new machine can mean greater efficiency, more sales, or a new product line, but it can also cut into your available floor space. Same with a new production line, a locker room, or a larger cafeteria space. That new machine is an additional cost and can cut into your available room.
Crowding more machines on the plant floor or reorganizing your operating space can also be a potential safety issue or cause motion waste. Employees must operate in tighter confines when there is less space on the plant floor. They may also need to move around the new equipment, leading to motion muda, or waste, that creates inefficiencies in production.
Luckily, there are potential solutions for reclaiming plant floor space.
How MODULAIR® Works
Compressed air is a critical utility for many manufacturers. Due to the frequent use of compressed air and the need for ductwork, many companies will find space on the shop floor for the compressors. This is convenient, reducing the need for ductwork. There is typically space for compressors, and maintenance is easier.
It’s a fine solution until the manufacturer needs space on the plant floor – valuable space the compressor uses.
MODULAIR® houses air compressors and dryer units using a pre-assembled modular system. The system is designed for easy installation and proper air compressor operation. It combines heavy-duty industrial construction with everything you need for simplified installation and proper operations.
Each module includes an air piping header system with individual compressor isolation valves for single-point customer connection. You have ductwork with gravity discharge dampers for hot compressor cooling air discharge and condensate piping with heat tracing for single-point copper tube connection. The air intake filtration system pre-filters the compressors, dryer cooling, and intake air. Automatic module temperature control is handled by thermostatically controlled and powered recirculation louvers, ductwork, and ventilation fans.
In addition, every module has electrical components, wiring and installation, lighting, 110V electrical outlets, space heaters, safety disconnects, a single-phase transformer, and an electrical pane. That’s all the equipment needed to properly operate your air compressor.
As a self-contained module, you can place it outside your main plant and facility, freeing up floor space, and reducing heat and noise while providing your facility with the compressed air you need.
Manufacturers that use MODULAIR® see additional benefits beyond just freeing up plant space:
- Lower maintenance costs and increased system reliability. You will save money by eliminating the need for maintenance and sanitization of the on-site compressors. The dedicated space, pre-engineered infrastructure, and easier access for compressor maintenance will increase reliability.
- With less crowding on the plant floor and less noise and heat generated by the air compressors in the working areas, there will be fewer injuries. You will have a safer and better work environment.
Getting Started with DIRECTAIR® and MODULAIR®
MODULAIR® is included with DIRECTAIR®, a compressed air utility service pioneered by OTC Industrial Technologies. With DIRECTAIR®, OTC will supply, install, operate, and maintain a new air compressor system designed around a compressed air strategy for your business. DIRECTAIR® customers pay only a monthly charge based on their compressed air and cooling water consumption.
If you have questions about DIRECTAIR® or want to discuss how MODULAIR® can free up plant floor space at your facility, contact OTC today. Let us know how we can help.
Stay up to date
SUBSCRIBE TO OUR BLOGPosts by Tag
- General Manufacturing (99)
- Compressed Air Solutions (54)
- Automotive (35)
- Finishing and Dispensing (31)
- Rotating Equipment (27)
- Industrial Automation (21)
- Maintenance & Repair Services (20)
- Case Studies (15)
- Electronics & Semiconductor (14)
- Sustainable Manufacturing (11)
- Energy Efficiency (10)
- Filtration (8)
- Energy, Power & Utilities (7)
- Food & Beverage (5)
- Oil & Gas (5)
- Pharmaceutical & Life Sciences (4)
- Industrial OEMs (3)
- Steel & Metal Manufacturing (3)
- Aerospace (2)
- Agriculture (2)
- Chemical & Petrochemical (1)
- Packaging & Processing (1)