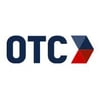
OTC Insights Team
Established in 1963, OTC Industrial Technologies (Ohio Transmission Corporation) is one of the largest industrial distributors & service providers in the United States. We're committed to seeing industrial operations advance through expert technical solutions & unmatched support using our years of experience.
In today’s fast-paced industrial landscape, every minute of uptime matters. Unscheduled downtime can be incredibly costly in terms of lost production, missed deadlines, and heightened costs of emergency repairs. Choosing a proactive approach to servicing and repairing your industrial equipment before issues happen proves to be an invaluable solution. By focusing on regular equipment maintenance and timely repairs, businesses can mitigate the hidden costs associated with downtime, optimize operational efficiency, and keep their competitive edge.
Let’s explore how regular service and repair can reduce the maintenance burden on your organization and address the hidden costs of downtime. See how OTC can help you keep your operations running at peak efficiency with customizable solutions and no territory or brand restrictions.
The Hidden Costs of Downtime
The last thing a business wants to see is a high amount of downtime. If your equipment fails without a plan in place, downtime has a domino effect that can impact nearly every aspect of your business in terms of:
- Lost Production and Missed Deadlines: When equipment is down, production stops. This often leads to delayed deliveries, potential contract penalties, and a loss of revenue.
- Increased Labor Costs: Emergency repairs may require overtime pay or specialized contract labor. Technicians who could focus on other tasks have to drop everything to fix the immediate issue.
- Damage to Customer Relationships and Reputation: Missed deadlines and altered delivery schedules can harm your brand’s reputation and break down customer trust. Customers depend on timely shipments, and repeated disruptions may prompt them to look elsewhere.
One study has shown that an hour of unplanned downtime can cost industrial facilities anywhere from thousands to hundreds of thousands of dollars, depending on the scale of their operations. By understanding these impacts, it becomes clear why minimizing downtime is so crucial.
Why Service and Repair is the Best Solution for Cost and Operational Efficiency
While replacing faulty or aging equipment might seem like the most effective fix, it often is more expensive in terms of capital expenditure, lead times, and reconfiguration of workflows. By servicing or repairing your equipment, you can often find faster turnaround times, lower costs, and lessened disruptions to your overall operations.
With expert service and repair providers like OTC, you have specialized knowledge at your disposal and ongoing support for your business to ensure your equipment is operating efficiently. We offer service and repair options for one-off repairs or customized service agreements with no territory or brand restrictions. Our plans are fully customized for each customer with no specific plans or pricing. We work with you!
Let’s dive deeper into the specific benefits a service and repair agreement can offer.
Benefits of Service and Repair for Industrial Equipment
Before writing off your equipment and replacing it with new equipment, consider the benefits of working with a partner like OTC for service and repair needs:
Cost Savings
- Lower Replacement Expenses: Instead of purchasing brand-new machines and taking on a high capital expense, repairs can restore your existing equipment to like-new conditions, allowing you to reinvest resources in more strategic areas for your business.
- Extend Equipment Lifespan: Routine maintenance and timely repairs prolong the operational life of your machinery, maximizing your initial investment.
- Reduce Staff Training: Restoring existing equipment removes the hassle of retraining staff and changing processes, which saves time and reduces risks associated with major system changes
Reduced Downtime
- Faster Repairs: With a dedicated service partner, emergency repairs can be handled more rapidly, often preventing production from grinding to a halt. Repairs are typically quicker than researching, ordering, and installing brand-new equipment, something that can be a burden on your staff.
- Critical Spare Parts: Maintaining spares and having a proactive repair plan ensures that when something does fail, replacement parts or components are readily available, keeping you up and running.
Enhanced Workflow Efficiency
- Preventative Maintenance: By detecting issues early through diagnostics and monitoring, you avoid breakdowns during peak production times, when you need reliability the most.
- Optimized Performance: Well-maintained machinery runs smoothly, uses resources more efficiently, and contributes to a safer working environment for employees.
Real-World Success of OTC Service and Repair
A Midwest Steel Stamping Plant came to OTC with a problem. Their continuous hydraulic cylinder failures caused significant downtime while the business was waiting for new cylinders to arrive.
Needing a solution to alleviate their downtime caused by hydraulic failures, they called on OTC to find a solution. OTC worked with the stamping plant on a repair program for the hydraulic cylinders. All ‘failed’ hydraulic cylinders were staged for OTC to pick up and manage the repairs for the plant. Upon completed repairs, the units were then stocked as critical spares to keep the operations running.
Result: With this new process, total plant downtime was minimized thanks to a ready supply of refurbished cylinders, and overall costs were reduced compared to buying new units.
How OTC Can Help Keep Your Business Running
OTC provides comprehensive service and repair solutions for industrial equipment with no territory or brand restrictions. With customizable agreements and one-off support, OTC can help keep your business running. We support a variety of industrial equipment service and repairs, including:
- Robotics: Arms, controllers, robot teach pendants, and electro-mechanical components.
- Hydraulics: Cylinders, pumps, actuators, and valves.
- Gearboxes, Drive Shafts, & U-Joints: Preventative maintenance, refurbishment, and vibration/noise reduction.
- Servo Motors: Diagnostics, customization, and repair for accurate positioning and speed control on AC and DC servos.
- Motor Repair: AC and DC motors and generators; explosion proof motor repair.
- Electrical Systems: Printed circuit boards, HMIs, VFDs, AMPs, PLCs, and teach pendants.
- Equipment Health Diagnostics & Monitoring: Vibration, temperature, torque monitoring, and speed.
Our customizable service agreements and 24/7 cloud-based remote monitoring also help you stay ahead of issues, reducing the risk of unplanned downtime. Our range of experts and stocked warehouses means we can quickly obtain and ship critical components, helping you maintain production schedules and meet customer demands.
Get Started with OTC Service and Repair Today
By focusing on proactive service and repair, you’ll see improvements in reduced downtime, cost savings, and increased efficiency. Our expert technicians are here to listen to your needs and discuss solutions to help you stay ahead in a competitive market. Let us handle your repair and maintenance needs so you can focus on growing your business.
Ready to take a more proactive stance on your industrial equipment maintenance? Contact OTC for a customized service agreement or one-off repair solution.
Stay up to date
SUBSCRIBE TO OUR BLOGPosts by Tag
- General Manufacturing (99)
- Compressed Air Solutions (54)
- Automotive (35)
- Finishing and Dispensing (31)
- Rotating Equipment (27)
- Industrial Automation (21)
- Maintenance & Repair Services (20)
- Case Studies (15)
- Electronics & Semiconductor (14)
- Sustainable Manufacturing (11)
- Energy Efficiency (10)
- Filtration (8)
- Energy, Power & Utilities (7)
- Food & Beverage (5)
- Oil & Gas (5)
- Pharmaceutical & Life Sciences (4)
- Industrial OEMs (3)
- Steel & Metal Manufacturing (3)
- Aerospace (2)
- Agriculture (2)
- Chemical & Petrochemical (1)
- Packaging & Processing (1)