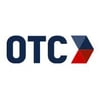
OTC Insights Team
Established in 1963, OTC Industrial Technologies (Ohio Transmission Corporation) is one of the largest industrial distributors & service providers in the United States. We're committed to seeing industrial operations advance through expert technical solutions & unmatched support using our years of experience.
Have you ever calculated the cost of downtime for your plant?
Additional maintenance fees, recurring machine problems, reduced efficiency, and lost and angry customers are hidden costs that may not be factored into the estimate. Eliminating those hidden costs requires improved equipment maintenance. Regularly scheduled maintenance reports give you only a brief snapshot of machine performance and reliability. The best way to reduce downtime and keep your machines running is through predictive reliability.
Predictive Reliability: Continuous Improvement for Equipment Maintenance
Going beyond traditional preventative maintenance programs, predictive reliability incorporates an asset management program and root cause analysis to drive continuous improvement in your asset uptime and reduce operating costs.
Preventative maintenance schedules can be an effective way to avoid downtime, but they come with drawbacks. If you’re performing maintenance on a recurring time schedule, you may be incurring downtime when no work is necessary. Alternatively, if an unexpected break occurs, your strict maintenance schedule might make it difficult to quickly adjust repair resources and apply them to the issue. Predictive maintenance and turnkey predictive reliability help avoid these unfortunate situations.
The Gap in Predictive Maintenance Strategies
Predictive maintenance uses technology, data modeling, and analytics to prevent future equipment failures. Technology like IoT (Internet of Things)-enabled sensors and devices continually monitor your equipment. Asset management programs digitally monitor and manage the program. When parts overheat or vibrate outside of suggested performance parameters, you receive automatic notifications. Instructions for correcting the issue are sent to the repair team, and work is done and logged in the program.
It handles the problem, but it's not driving or supporting improvement. In addition, there are gaps in the implementation.
As a maintenance leader, you may be struggling to have IT configure your monitoring device. Accessing the data, or setting up alerts, may also be problematic — a sensor is only as good as the data that is collected and is accessible. Additionally, coordinating with software companies, selecting the hardware suppliers, and finding repair experts who can be on call and who understand your equipment aren't easy tasks.
The struggle with predictive maintenance is the piecemeal nature of the solution. It's not focused on continuous improvement, just catching problems early. A single shop floor may have hundreds of machines, requiring a multitude of hardware and software solutions to monitor. That’s where a turnkey predictive reliability solution can help.
Introducing Predictive Reliability and OTC’s AiM
Predictive maintenance is only one component of a complete solution for continuous maintenance improvement. Do you have a plan for setting up the predictive maintenance equipment? What software and hardware will you use? When a problem occurs, how are you going to handle it? How do you use the information you are collecting to make data-driven decisions regarding equipment and maintenance? Putting all these pieces together for optimized uptime and reduced operational costs is the goal of predictive reliability.
OTC’s Automated Intelligence for Maintenance (AiM) solution offers turnkey predictive reliability. It’s an end-to-end technology and engineering solution leveraging industry-leading vibration and sensor products to give you automated intelligence and analytics for maintenance. It includes local, proactive repair solutions to streamline rapid repairs when they are needed, minimizing unscheduled downtime.
AiM sets up feedback loops across the maintenance and asset management to drive continuous improvement. Working with the team, you identify the root cause of equipment and maintenance issues and then implement solutions that sustainably address and correct the problems. With a single team handling the work, you can improve monitoring, streamline data collection, create dashboards, and increase focus on problem-solving. That's reliability.
The Benefits of Predictive Reliability
Predictive reliability through AiM significantly decreases downtime and lost productivity, reduces escalated repair costs, and takes the hassle and complexity out of implementing predictive maintenance and reliability programs. AiM is the only true end-to-end, completely customizable condition monitoring system, remote MaaS (Monitoring as a Service), repair and support services solution on the U.S. market today.
OTC’s AiM service is completely customizable and configured to your needs. It includes:
- Best-in-class, reliable hardware components
- Hydraulic Institute-certified system assessment
- On-site installation and testing
- Complete customization for your applications, including component configuration and programming
- Cloud-based dashboard for real-time data and historical data storage
- Secure, high-speed wireless service or connection to your IT network
- 24/7 remote MaaS by the team that designed and installed your system
- OEM-certified equipment maintenance and repair services
This means that AiM is a complete solution for predictive maintenance — from design and installation to custom programming and configuration, to managing the program and expert repair. It’s true turnkey predictive reliability.
A Closer Look at OTC's AiM
At the frontline of the AiM solution is our partnership with industry-leading vibration companies and their remote monitoring solutions. With OTC and AiM, you can find the sensor and solution that's right for you, including:
Vibration sensors
Monitoring vibration levels is one of the easiest ways to detect potential problems. Many facilities experience constant vibration due to the sheer size of the system and all the moving parts involved. With vibration sensors, it’s easy to see changes in vibration levels that could indicate a problem.
Oil sensorsContaminated oil can be extremely corrosive and negatively impact the health of your system. Oil sensors can instantly set off an alarm when there are contaminants or dangerous changes in oil temperature.
Thermal camerasHeat is an invisible threat that can wear down your tools. With wireless thermal cameras in place to monitor unexpected rises in temperature, this threat is easy to identify and deal with before it becomes a problem.
Pressure sensors
These sensors monitor equipment and system pressures to determine if they are operating as designed or required. Additionally, they ensure the equipment is operating in stable pressure-operating conditions.
Motor amperage
Motor amperage detectors monitor motor performance by amperage to ensure it is operating in a stable condition.
Slow motion amplification
This video processing method provides a visual of the equipment, piping, and foundation. It is used to measure any excessive movements or strains based on system demands.
Wireless convertersThese converters change wired sensors into wireless, making it easy to transmit important data about your system’s health to anywhere in your facility.
Analytical softwareWith an all-in-one dashboard, you save time while staying informed of any relevant changes in the health of your equipment.
What Can Predictive Reliability Do for You?
Through technical integrations and smart asset management, you can expect to reduce downtime by as much as 80%.
Rather than accepting downtime and equipment repairs as a normal cost of production, take control of your machine health with OTC and AiM and drive continuous improvement. You’ll have access to relevant data for better machine and equipment decisions, with a solution designed around your needs. Rest easy knowing that before a problem happens, you have a team monitoring your equipment 24/7 and experts locked in place and ready to get your operations up and running as quickly as possible.
End-to-end maintenance and repair services based on data, remote monitoring, analytics, and the latest technology — that’s predictive reliability. Here are a few of the other benefits you can expect from AiM over other maintenance solutions:
Seamless Integrations with Your Existing System
One of the best parts of AiM is how easily it works with existing hardware. Unlike other solutions, you don’t need to perform complex installations or change the tools you already work with. With seamless integrations into your current operation, you can start monitoring the health of your operation within hours.
Stay Informed of Your Equipment’s Status
Ensure you get the best ROI on your equipment. Manufacturing equipment isn’t cheap, and you expect exceptional performance. Early detection allows you to prevent small issues from becoming problems that cause serious breakdowns.
Design Better Maintenance Schedules
Stop performing unnecessary maintenance. With better data come better repair schedules. When you know that your entire operation is running at 100%, you’re able to avoid downtime that could slow down your business and affect your bottom line.
Own Your Data
Unlike other predictive reliability solutions, with OTC AiM, you own all your data. That means you have complete control over how your critical system information is shared, used, and distributed. With a comprehensive dashboard and analytical reporting software, you’ll feel more in control than ever before when you work with AiM.
Discover All the Ways OTC Can Help
Downtime and maintenance issues are costly and frustrating. In the past, there wasn’t an easy solution for optimizing uptime with predictive maintenance. OTC’s AiM is changing that for manufacturers with our predictive reliability.
Contact OTC and our experts today to see how we can help.
Stay up to date
SUBSCRIBE TO OUR BLOGPosts by Tag
- General Manufacturing (99)
- Compressed Air Solutions (54)
- Automotive (35)
- Finishing and Dispensing (31)
- Rotating Equipment (27)
- Industrial Automation (21)
- Maintenance & Repair Services (20)
- Case Studies (15)
- Electronics & Semiconductor (14)
- Sustainable Manufacturing (11)
- Energy Efficiency (10)
- Filtration (8)
- Energy, Power & Utilities (7)
- Food & Beverage (5)
- Oil & Gas (5)
- Pharmaceutical & Life Sciences (4)
- Industrial OEMs (3)
- Steel & Metal Manufacturing (3)
- Aerospace (2)
- Agriculture (2)
- Chemical & Petrochemical (1)
- Packaging & Processing (1)