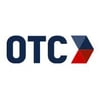
OTC Insights Team
Established in 1963, OTC Industrial Technologies (Ohio Transmission Corporation) is one of the largest industrial distributors & service providers in the United States. We're committed to seeing industrial operations advance through expert technical solutions & unmatched support using our years of experience.
Waiting for something to break is never a good idea, especially in manufacturing. Even a few minutes of downtime can delay shipments, bite deep into margins, and cause issues up and downstream in your processes, not to mention the stress and pressure it can put on your team. With proper preventative maintenance procedures and schedules, you can keep your manufacturing facility moving, avoid critical downtime, and prevent costly problems.
What Is Preventative Maintenance?
Simply put, preventative maintenance is when you perform scheduled repairs, replacements, and calibrations on a machine or piece of equipment. Every tool, from an air compressor to a pump, is different, so how often you need to perform this maintenance can vary depending on the type of work it does. Understanding manufacturer specifications can help you create schedules for maintenance plans and keep your equipment in working order.
Preventative maintenance can also be used to address ongoing and recurring problems with production equipment. For example, if a pump regularly shuts down or the motor runs loud, then increasing the frequency of maintenance or adding a specific mitigation activity might increase uptime and reduce repair costs.
Here are a few types of preventative maintenance that you may want to explore.
Maintenance Based on Use
When creating a maintenance schedule, one of the first things to decide is when maintenance is necessary. Depending on the type of machine in question, it may make more sense to perform these repairs on a set schedule, or after the machine has been in use for a set amount of time.
Maintenance based on use is a method that determines repair times based on how long the machine has been running. In industries like oil and gas where residue can build up during extended use periods, it often makes sense to schedule checks after 10 or more hours of operation. This strategy is effective for equipment that experiences heavy wear and tear during use but doesn’t change much outside of working hours.
Manufacturer-Recommended Maintenance Schedules
While inspecting your tools manually is a good practice, following the equipment manufacturer’s recommended maintenance schedule is often the best strategy. When working with experienced suppliers like OTC Industrial Technologies, experts will walk you through recommended maintenance procedures and ensure you have the tools you need.
Taking the time to discuss these procedures with experts not only gives them an opportunity to better understand your business, but also ensures that you get the most out of your equipment. For consultations or repairs to critical equipment, consider using a field service team. Field service teams come directly to your jobsite to perform repairs, giving you and your maintenance team access to the experts that understand how to keep your equipment in working order.
Continuous Maintenance
Continuous maintenance is a type of preventative maintenance that occurs on a daily, if not hourly, schedule. It includes oiling gears, replacing disposable parts, monitoring performance, and running frequent tests. Manufacturing is a precise industry, so if you need peak performance from your equipment 24/7, developing continuous, daily maintenance schedules can help.
The Advantages of Preventative Maintenance
Preventative maintenance schedules can mean a lot of work for you and your team, but the endeavor is worth it. The manufacturing industry relies on expensive, difficult-to-replace equipment, and performing maintenance is easier than outright replacing a machine. Here are a few of the major benefits of developing a preventative maintenance schedule.
Preventing Breakdowns
Losing an essential machine can mean downtime, which is the death of a manufacturing operation. When parts break, production stops, and your team can quickly find themselves out of a job. While rental replacements can provide a temporary fix, it’s much better to perform maintenance before repairs become necessary and to catch an issue before it becomes downtime.
Extending the Life of Your Equipment
High-quality manufacturing equipment isn’t cheap. When you buy a machine, you want to get the most out of it. Preventative maintenance can ensure your machines work at optimal efficiency, and with a strong maintenance program, you can boost the lifespan of your equipment and see more output from the investment you make in the machine.
Increasing Efficiency
Many facilities wait to perform repairs until something breaks. While preventing these breakdowns is an important part of preventative maintenance schedules, it isn’t the only benefit. Before a machine breaks, it typically works at a lower capacity or efficiency. Regular repairs prevent these slowdowns from occurring and make sure you get the most value out of your equipment.
Creating a Safer Workplace
Broken and poorly maintained machines are dangerous and can be an accident waiting to happen. Maintenance schedules not only improve the life of your equipment, but they help keep your team safe as well. Unexpected breakdowns can have disastrous consequences. You don’t want your essential safety equipment to experience a failure during a critical moment in the manufacturing process. Creating a regular repair schedule prevents this worst-case scenario from happening.
Discover All the Ways OTC Can Help
You understand what it’s like to be an expert in your industry, so work with a team that’s an expert in preventative maintenance, service, and repairs. With decades of experience working with critical finishing, electrical, automation, and pumping equipment, OTC knows how to get the most mileage out of your purchase.
Whether you need help creating a maintenance schedule for the first time or just want a second opinion on your current maintenance program, OTC can help. Our experts have decades of experience in the manufacturing industry and can help you design a system that works. With dedicated resources for handling preventative maintenance, service shops focused on timely and accurate repairs, we ensure maximum uptime for your machines and equipment.
Want to see how we do it? Contact us today for a consultation to discuss your specific needs.
Stay up to date
SUBSCRIBE TO OUR BLOGPosts by Tag
- General Manufacturing (99)
- Compressed Air Solutions (54)
- Automotive (35)
- Finishing and Dispensing (31)
- Rotating Equipment (27)
- Industrial Automation (21)
- Maintenance & Repair Services (20)
- Case Studies (15)
- Electronics & Semiconductor (14)
- Sustainable Manufacturing (11)
- Energy Efficiency (10)
- Filtration (8)
- Energy, Power & Utilities (7)
- Food & Beverage (5)
- Oil & Gas (5)
- Pharmaceutical & Life Sciences (4)
- Industrial OEMs (3)
- Steel & Metal Manufacturing (3)
- Aerospace (2)
- Agriculture (2)
- Chemical & Petrochemical (1)
- Packaging & Processing (1)