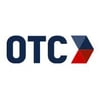
OTC Insights Team
Established in 1963, OTC Industrial Technologies (Ohio Transmission Corporation) is one of the largest industrial distributors & service providers in the United States. We're committed to seeing industrial operations advance through expert technical solutions & unmatched support using our years of experience.
Finding the most reliable and cost-effective solution for your operation’s compressed air needs can take time. You need to understand your needs and requirements, research your available options, perform price analyses, and discuss strategies with potential vendors.
While researching these services, one inevitable question will quickly come up — are you better off renting a compressor, purchasing a new compressor, or working with a compressed air utility service?
What Is a Compressed Air Utility Service?
A compressed air utility service treats compressed air like more traditional utilities such as gas, water, and electricity. You purchase clean, reliable compressed air directly, rather than purchasing the equipment to provide the air. When working with a compressed air utility service like DIRECTAIR®, an expert assesses your compressed air needs and develops a solution that matches your business. For the DIRECTAIR® service, this includes installing the necessary machines on-site, and implementing a monitoring system to ensure optimal performance of the equipment.
You don’t have to worry about the equipment or maintenance. The provider will assess your needs and requirements and use the right machines to get the job done. They offer expert care and maintenance schedules that help you maximize your operation’s uptime. Compressed air utility services are all-in-one packages that provide assessments, equipment, and maintenance for a single monthly fee. In addition, the expense for the service is overhead, rather than a capital expense. Budgeting for the service is also more consistent and stable, eliminating unexpected maintenance charges and dependent entirely on use.
Rental Compressed Air and Manufacturing
When you rent an air compressor, you get access to the machine for a monthly cost. This compressor could be used to manage a spike in compressed air needs or production, or to evaluate if production needs additional compressed air capacity. Rental units provide flexibility, with the machine being returned, and the expense removed, when the need is done.
There are a few things to consider when renting. Renting doesn’t include an assessment of your needs or a guaranteed maintenance schedule. When you rent equipment, you pay a flat monthly fee, but may be responsible for any necessary repairs or maintenance. Additionally, you are not guaranteed to have access to industry experts who understand how to perform these repairs.
Purchased Compressed Air Units and Manufacturing
Many manufacturers choose to purchase a compressed air unit, taking on the risk and advantages of ownership. The unit is maintained by the on-site maintenance staff, and there are little to no restrictions on use. A new unit is a capital expense, and the value depreciates over time, providing budgetary advantages.
There are risks associated with owning a compressed air unit. Maintenance and upkeep on the unit is, ultimately, the responsibility of the owner. For some staff, where maintenance resources are tight or there isn’t compressed air expertise on site, this can be problematic, with reliability of the units depending on maintenance resources. In addition, the costs for repairs and maintenance may exceed budgeted amounts, and additional systems like a cooler or drying unit may be necessary.
Advantages of Compressed Air Utility Services
Many manufacturers may not be aware of DIRECTAIR® and the advantages of a compressed air utility service.
Relying on a compressed air utility service for your operation’s compressed air needs can be an excellent choice for businesses that want a consistent supply of compressed air without any surprises. These services come with greater peace of mind, allowing the on-site team to focus on production rather than the compressors. Here are a few of the main advantages of working with a compressed air utility service.
Improved Reliability
When working with a compressed air utility service, you have consistent access to industry experts who can help maintain the health of your equipment. These services assess your operation’s needs and provide you with the compressors that can give you the best results. Additionally, you can rely on experts to install and maintain your equipment, rather than spending internal resources.
Consistent Pricing
Compressed air utility services offer all-in-one packages. When you rent or purchase equipment, you pay a base fee but may also be responsible for repair costs or any damage to the machine. These unexpected costs can bite deep into your budget. Working with a compressed air utility service provides you with a predictable cost that makes it easier to determine your expenses and the expected ROI.
Easier Maintenance
These services come with dedicated maintenance professionals who are always available to perform repairs on your equipment. Compressed air utility services don’t leave you with the burden of expensive repairs if something goes wrong. Relying on industry experts to maintain and repair your air compressor takes the stress out of traditional rentals.
Reduced Energy Costs
Allowing DIRECTAIR® experts to assess your compressor needs results in the selection of more efficient equipment and better installation. These benefits result in lower overall energy costs. Reducing your energy costs is a great way to meet ESG goals, and can provide a variety of benefits to your operation such as more predictable expenses and better operational data.
More Time for Your Team
When renting equipment, installation and maintenance responsibilities fall on your staff. When working with a compressed air utility service, you don’t need to worry about the increased strain on your employee hours. During times when maintaining a labor force can be a struggle, the additional worker capacity can be an advantage.
Contact the Experts to Find the Option That’s Right for You
If you aren’t sure how to decide between renting a compressor, purchasing one, or working with a compressed air utility service, the experts at OTC can help. Our team has a proven track record of helping companies find the right machine for their operation, and we’d love to show you how we do it. To learn more about the differences between these services, or about all the other ways we can help, contact OTC today.
Stay up to date
SUBSCRIBE TO OUR BLOGPosts by Tag
- General Manufacturing (99)
- Compressed Air Solutions (54)
- Automotive (35)
- Finishing and Dispensing (31)
- Rotating Equipment (27)
- Industrial Automation (21)
- Maintenance & Repair Services (20)
- Case Studies (15)
- Electronics & Semiconductor (14)
- Sustainable Manufacturing (11)
- Energy Efficiency (10)
- Filtration (8)
- Energy, Power & Utilities (7)
- Food & Beverage (5)
- Oil & Gas (5)
- Pharmaceutical & Life Sciences (4)
- Industrial OEMs (3)
- Steel & Metal Manufacturing (3)
- Aerospace (2)
- Agriculture (2)
- Chemical & Petrochemical (1)
- Packaging & Processing (1)