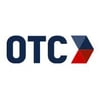
OTC Insights Team
Established in 1963, OTC Industrial Technologies (Ohio Transmission Corporation) is one of the largest industrial distributors & service providers in the United States. We're committed to seeing industrial operations advance through expert technical solutions & unmatched support using our years of experience.
The start of a new year brings new business opportunities, new challenges, and new practices that can make or break your business.
For the manufacturing industry, this means ensuring that you are up to date on evaluating new technologies, identifying possible opportunities for a competitive advantage, and reviewing what steps the competition is taking and how you will respond.
Compressed air, a core utility for most manufacturers, is one area that requires your attention, especially in the upcoming year when we can expect energy cost disruption and market demands to increase. In fact, compressed air is often one of the most power-hungry systems in manufacturing operations. In this article, we’ll look at a few trends that will impact compressed air in the coming year.
Advancements in Compressed Air Systems and Units
As technology advances, compressed air systems have become more advanced and energy efficient. While the average person may not consider the many options for air compressors, these machinery updates are necessary to focus on energy efficiency and manufacturing.
Advancements in compressed air allow for a quieter operation. The quieter operation allows for a safer, more effective work environment for employees who must use compressed air to operate machinery. Additionally, safety restrictions may impact where and how you can place your compressor, and quieter operations may allow more options when planning your workspace.
Finally, more advanced oil-free air compression systems, which require less maintenance and often cost less than other systems, may be able to handle and meet larger operational requirements, requirements that once required oil-based machines. Make sure to investigate oil-free options when evaluating a new system.
The Impact of Supply Chain Disruption
Manufacturers, and the market in general, are still struggling with the impact of supply chain disruption.
This means that new compressors and compressor parts that were once readily available may be on backorder. Rush and emergency orders may be significantly more expensive than they once were.
To overcome these challenges, it’s important to evaluate current operations, plan for future needs, and look at alternative solutions when necessary.
For current operations, look at units that see frequent downtime or higher repair costs. In cases like this, you may need to order a new unit early, even if the older unit is providing some capacity and uptime. Order parts that are frequently used and set up a more regular maintenance schedule to identify problems early.
For future needs, set goals for your facility and see if your current compressed air can meet them. If it can’t, start planning to upgrade early, before a backordered unit sets production and orders behind. Utilizing monitoring for your compressed air or conducting an air audit can provide valuable usage data. Variable speed compressors and rental units may be able to meet temporary capacity requirements, but keep in mind these aren't long-term solutions. It may not feel comfortable, but you may have to make tough purchasing decisions now to meet your production and business goals.
In these difficult times, it’s a good idea to evaluate alternative solutions for your compressed air needs. Long-term rental units, for example, may be necessary to meet an uptick in orders or demand for compressed air. Another alternative solution may be purchasing compressed air as a utility rather than buying a new compressed air unit using the DIRECTAIR® service.
DIRECTAIR® Compressed Air Utility Service
While many manufacturers are experts in production and manufacturing operations, they don’t have the expertise necessary to optimize and maintain their compressed air service.
This is where DIRECTAIR® comes in. With DIRECTAIR®, manufacturers pay only for the compressed air and power that they use. Like other utility services, such as electricity and water, an outside service company sets up, maintains, and provides compressed air. The outside company, in this case, DIRECTAIR®, handles the installation of the air compressor units on the site. It handles upkeep, monitoring, and maintenance. The manufacturer pays DIRECTAIR® for the compressed air and provides power for the unit. This means:
- No repair or maintenance expenses.
- A constant supply of clean compressed air.
- No downtime for the compressed air system.
- Lower energy costs as the provider uses newer, more energy-efficient units.
As manufacturers struggle with older compressed air units and shifting production needs, working with a utility provider like DIRECTAIR® makes sense, providing long-lasting benefits and allowing the manufacturer to shift maintenance crews from the old and unreliable compressor units to more valuable work.
Planning a Successful Year for Manufacturers
For many manufacturers, production runs on compressed air. This is true across a broad spectrum of manufacturing verticals, from semiconductors to the food and beverage industry.
Success in the new year depends on reliable uptime and efficient use of systems like compressed air. If you have questions or concerns about what you can do to improve the uptime or reliability of your compressed air or want to look at options for upgrading or improving your service, then set up a no-obligation discussion with OTC Industrial Technologies.
Our experts have been delivering results for many of the most demanding applications that rely on compressed air. Set your production team up for success in the new year with OTC.
Stay up to date
SUBSCRIBE TO OUR BLOGPosts by Tag
- General Manufacturing (99)
- Compressed Air Solutions (54)
- Automotive (35)
- Finishing and Dispensing (31)
- Rotating Equipment (27)
- Industrial Automation (21)
- Maintenance & Repair Services (20)
- Case Studies (15)
- Electronics & Semiconductor (14)
- Sustainable Manufacturing (11)
- Energy Efficiency (10)
- Filtration (8)
- Energy, Power & Utilities (7)
- Food & Beverage (5)
- Oil & Gas (5)
- Pharmaceutical & Life Sciences (4)
- Industrial OEMs (3)
- Steel & Metal Manufacturing (3)
- Aerospace (2)
- Agriculture (2)
- Chemical & Petrochemical (1)
- Packaging & Processing (1)