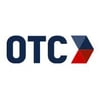
OTC Insights Team
Established in 1963, OTC Industrial Technologies (Ohio Transmission Corporation) is one of the largest industrial distributors & service providers in the United States. We're committed to seeing industrial operations advance through expert technical solutions & unmatched support using our years of experience.
If recent years have taught us anything, it’s how important it is to have a robust solution for supply chain disruptions.
If you don’t have access to your parts and supplies, then your operation grinds to a halt. You can’t manufacture, employees don’t have work, and you’re forced to stop helping your customers. This can be deadly for any business, so don’t wait to take the necessary steps to avoid these costly interruptions.
How to Avoid Supply Chain Disruptions
Avoiding supply chain issues is easier with the right partners, the right planning, and the right strategy. Understanding what strategies work to avoid these problems helps you keep your business moving while avoiding costly delays. Some approaches are better than others, so working with a variety of solutions can help insulate your business from these dangers.
Here are five ideas you can use to help avoid supply chain disruptions.
1. Partner With Suppliers
One of the best ways to reduce the impact of supply chain disruptions is to partner with a supplier. If you develop a good relationship with your supplier, then they are more likely to work with you and find a solution when facing critical supply shortages. They can act as your agent in the marketplace. At the very least, if you’ve partnered with a supplier, they can let you know of any upcoming shortages. Suppliers like OTC Industrial Technologies do more than just provide you with parts; they take the time to learn about your business and develop plans that keep you safe from these shortages.
2. Implement Regular Maintenance Schedules
Regular maintenance schedules are a crucial part of any operation, but they are especially important when faced with supply chain shortages. Running an automobile OEM, you know what happens when a part breaks down with no replacement. Work stops and your bottom line suffers. If you haven’t already, start using preventative maintenance to cut down on unexpected downtime and increase overall efficiency.
Understanding when you will need replacement parts for critical supplies such as filters, belts, or even complex and critical automation equipment helps you plan around potential supply chain disruptions. Performing regular equipment evaluations is essential as it gives you time to source complex parts. If you aren’t sure how to create an effective maintenance schedule, contact OTC. Our experts know what it takes to get the most out of your equipment and can help you plan around potential disruptions.
3. Leverage Your Production Data
Data is king. By using your production data and forecasting your schedule, you can plan out shipments and orders to avoid missing parts and equipment while also avoiding the high cost of extra inventory. With better data and an accurate part and product forecast, you can work with OTC to place orders early - ensuring you have what you need before you need it. For example, if you know that filters need to be changed monthly, then purchase additional filters when there is a supply and the cost is low. Keep an adequate supply on hand to avoid paying extra when the price is high. The same with other materials.
Similarly, by collecting machine data like heat or cycle speed, you can better know when a machine needs maintenance to avoid purchasing replacement parts. A managed compressed air service like DIRECTAIR® not only ensures you have guaranteed compressed air at the volume, flow, and dew point you need, it can provide additional production data. For example, tracking the volume of air used for pneumatic machines gives you an idea of the pressure your equipment is facing.
With better data and an accurate forecast, you can easily plan shipments months in advance. Many suppliers operate on a first-come, first-served basis, so placing your orders early lets you get a foot in the door while others are left in the cold.
4. Work With a Dedicated Distributor
Navigating the complex sea of suppliers, manufacturers, and shipping companies can take time out of your day and leave your head spinning. If you don’t have the time to dig through shipping orders and compare the rates of different suppliers, working with a dedicated distributor can help. Distributors like OTC have relationships with suppliers that you can benefit from. These relationships lead to more effective communication and collaboration, which helps you plan for your future needs.
5. Identify Which Parts Need to Be Replaced Early
Even the most reliable parts can fail. While preventative maintenance schedules ensure you get the most out of every machine, sometimes replacements need to be made. Rather than wait for a breakdown that cripples your operation, you should try to detect these replacements early. Look at tracking output and machine data with a predictive system to automatically detect when there is a potential problem. Early detection gives you time to contact suppliers, browse new equipment, and even find rental equipment that can prevent you from experiencing delays.
Discover All the Ways OTC Can Help
If you’re worried about the impact of supply chain disruptions, OTC can help.
Our experts don’t just know how to find replacement parts quickly, they know what it takes to prevent breakdowns from occurring in the first place. If you want to learn more about how you can protect your business from these serious issues, contact us today.
Stay up to date
SUBSCRIBE TO OUR BLOGPosts by Tag
- General Manufacturing (99)
- Compressed Air Solutions (54)
- Automotive (35)
- Finishing and Dispensing (31)
- Rotating Equipment (27)
- Industrial Automation (21)
- Maintenance & Repair Services (20)
- Case Studies (15)
- Electronics & Semiconductor (14)
- Sustainable Manufacturing (11)
- Energy Efficiency (10)
- Filtration (8)
- Energy, Power & Utilities (7)
- Food & Beverage (5)
- Oil & Gas (5)
- Pharmaceutical & Life Sciences (4)
- Industrial OEMs (3)
- Steel & Metal Manufacturing (3)
- Aerospace (2)
- Agriculture (2)
- Chemical & Petrochemical (1)
- Packaging & Processing (1)