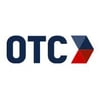
OTC Insights Team
Established in 1963, OTC Industrial Technologies (Ohio Transmission Corporation) is one of the largest industrial distributors & service providers in the United States. We're committed to seeing industrial operations advance through expert technical solutions & unmatched support using our years of experience.
Manufacturing batteries for electric vehicles is a complex process that requires specialized equipment to operate efficiently. Your facility contractor or engineering team may not have access to the expertise and resources necessary to optimize or even design the facility for efficiency.
To stay on the cutting edge of the industry, you need a partner who can provide you with the right experience and knowledge to ensure success.
The Move Toward Electrification
Electric vehicles are here to stay. In recent years, the shift from traditional internal combustion engines (ICEs) to electric vehicles (EVs) has been undeniable. While ICE vehicles still make up the majority of cars on the roads today, the actions of large automobile manufacturers make it clear where the industry is headed.
With these trends in mind, it’s an opportunity for manufacturers to build new facilities to fill orders for new vehicles or build replacement EV batteries.
What Does It Take to Manufacture an EV Battery?
Whether designing and building a new location to manufacture EV batteries or planning a renovation of an existing facility, understanding the equipment necessary for optimizing production helps you get set up for success.
The Components and Materials in an EV Battery
Most EV batteries are high-capacity lithium-ion. These batteries allow electric cars to be recharged with minimal energy loss.
The battery uses graphite or carbon, metal oxide, and lithium salts. These make up the core components of the battery, the anode, cathode, electrolyte, separator, and lithium-ions. These are combined to create positive and negative electrodes that, when connected by the electrolytes, create the electric current that is the energy for the car.
Processing the Raw Materials for an EV Battery
It is challenging and expensive to process the raw materials for EV batteries.
On average, the battery in an electric vehicle is made from raw materials that include an estimated 77 pounds of nickel, 44 pounds of manganese, 30 pounds of cobalt, and 17 pounds of lithium carbonate. All these materials need to be found and then extracted or mined from the Earth, which is costly and potentially damaging to the environment.
It’s estimated that a single ton of lithium ore requires 500,000 gallons of water. Depending on the extraction method, it can use as much as a million gallons of water for a single pound of lithium.
Already, experts are working on finding new sources for the materials used in manufacturing lithium-ion batteries. However, it can take 7 to 10 years to open a new mine so, for now, supplies are limited.
Manufacturing an EV Battery
Due to the high demand for batteries, as well as the high cost of the materials, it is important to optimize the manufacturing process as much as possible when designing and building a new facility.
Automation and Robotics for EV Batteries
Look closely at how to automate as much of the facility as possible. This includes systems such as robotics and assembly lines. Not only is this safer for handling potentially toxic materials, but it can reduce waste and increase efficiency and productivity.
Sensors and Data Collection for EV Batteries
Collecting data and having clean and complete build records, production reports, and compliance records are critical for EV batteries. Any problems or safety issues need to be tracked to the source during production so they can be corrected or to prevent the issue in the future. Look at integrating a complete tracking system. The goal should be end-to-end traceability for every product built in the facility.
Facility Design for EV Batteries
As a new and still developing technology, the process for manufacturing EV batteries will likely change. New systems or components will be added, or new build methods will be implemented. This will require adaptability and flexibility in manufacturing processes and facilities. Look at using adaptable components in your new facility. Rather than static designs, incorporate modular systems that can be adjusted when needed.
Compressed Air for EV Batteries
Compressed air is critical for EV battery manufacturing. An energy-efficient system that provides clean, reliable compressed air can greatly benefit efficient production. You also have multiple options for the system. Rather than installing the air compressors on the production floor, look at setting them up in a separate building with the hook up to the production area. There are also options for using a compressed air service for the new facility, avoiding capital costs and increasing the reliability of compressed air.
The Keys to Success for Manufacturing EV Batteries
Complex manufacturing requires a facility and production area designed to support it. That starts by working closely with manufacturing and production experts as you design and build your facility.
Work with our production and equipment experts for deep and extensive knowledge across all areas of industrial and manufacturing needs. See what our team at OTC Industrial Technologies can offer for all of your facility needs.
Stay up to date
SUBSCRIBE TO OUR BLOGPosts by Tag
- General Manufacturing (99)
- Compressed Air Solutions (54)
- Automotive (35)
- Finishing and Dispensing (31)
- Rotating Equipment (27)
- Industrial Automation (21)
- Maintenance & Repair Services (20)
- Case Studies (15)
- Electronics & Semiconductor (14)
- Sustainable Manufacturing (11)
- Energy Efficiency (10)
- Filtration (8)
- Energy, Power & Utilities (7)
- Food & Beverage (5)
- Oil & Gas (5)
- Pharmaceutical & Life Sciences (4)
- Industrial OEMs (3)
- Steel & Metal Manufacturing (3)
- Aerospace (2)
- Agriculture (2)
- Chemical & Petrochemical (1)
- Packaging & Processing (1)