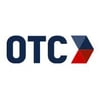
OTC Insights Team
Established in 1963, OTC Industrial Technologies (Ohio Transmission Corporation) is one of the largest industrial distributors & service providers in the United States. We're committed to seeing industrial operations advance through expert technical solutions & unmatched support using our years of experience.
Finishing, while essential for many manufacturing processes, can be expensive and inefficient. A significant cause of that inefficiency and added expense is compressed air. Compressed air is widely used in industrial applications like finishing and is a substantial energy expense.
There are steps manufacturers can take to increase efficiency and reduce the cost of the compressed air used in finishing.
Compressed Air in Manufacturing
A steady source of compressed air is critical for many production processes, but manufacturers often don’t realize how much efficiency is lost or how costs are increased due to poorly designed or maintained compressed air systems. This is especially true for finishing, where paint can be wasted and quality hurt due to inconsistent or improperly managed compressed air operations.
Inefficient compressed air usage can quickly eat into your budget. If your spray booth has a leak or is not distributing air evenly, or your cleaning station uses more PSI than required for the job, then you’re generating waste.
An air audit can help you find, and then correct, those areas of waste.
An Air Audit for Finishing Operations
An air audit is a professional examination of your compressed air operations and systems. It is performed at your manufacturing facility or jobsite. An air audit is a thorough assessment of the way you use your compressed air, including the entire finishing process. The compressed air expert will analyze the overall efficiency of the system and identify any concerns that may impact efficiency or create waste. Commonly found issues include:
- Leaks and poor piping
- Old or poorly maintained equipment
- Improper equipment usage
- Uneven pressure distribution
Additionally, air audits help you determine exactly what your demand requirements are.
The information collected during an air audit will allow you to make an informed and data-driven decision regarding improvements to your compressed air system. Whether you’re looking to build a new system, upgrade your current compressed air processes, or just uncover potential areas of waste, an air audit pays for itself.
Increase the Efficiency of Your Compressed Air System for Finishing
After receiving your air audit report, there are several steps you can take to improve your compressed air performance, increase efficiency, or reduce energy consumption in your finishing processes. These could include:
- Purchasing New Compressors
Depending on your operations and usage, you may find a new air compressor will deliver a rapid ROI and immediate benefits. As a trusted provider of air compressors, OTC can help you replace old equipment that is causing waste in your facility. After receiving your air audit, you’ll have a better understanding of precisely what your requirements are, and an OTC expert can recommend a compressor that meets your needs and budget.
2. Utilizing Rental UnitsIf, in the air audit, you find that your current compressors need to be repaired, or you are struggling with surges in usage, then you may need to consider rental air compressors. When a compressor fails or it needs to go down for maintenance and repair, production can stall. To avoid a costly disruption and manage production flow, consider having a partner like OTC that owns the largest rental fleet of air compressors in the country.
3. A Turnkey Solution with DIRECTAIR®In many cases, especially for manufacturers that rely on high-volume compressed air, OTC’s DIRECTAIR® product may be the best and most economical solution. It provides compressed air utility services with guaranteed uptime, and it is managed remotely by the experts at OTC. Rather than struggling with capital expenses or unexpected repair costs, with OTC's FOURTH UTILITY™ compressed air service you pay only for the air you use.
Discover All the Ways OTC Can Help
With so many options for compressed air solutions, it’s critical to have the data on hand before you make a decision. That’s the benefit of starting with an air audit.
Want to learn more about OTC’s compressed air services for finishing and dispensing? We can help. To discuss your needs or set up a time to meet with one of our compressed air experts, contact us today.
Stay up to date
SUBSCRIBE TO OUR BLOGPosts by Tag
- General Manufacturing (99)
- Compressed Air Solutions (54)
- Automotive (35)
- Finishing and Dispensing (31)
- Rotating Equipment (27)
- Industrial Automation (21)
- Maintenance & Repair Services (20)
- Case Studies (15)
- Electronics & Semiconductor (14)
- Sustainable Manufacturing (11)
- Energy Efficiency (10)
- Filtration (8)
- Energy, Power & Utilities (7)
- Food & Beverage (5)
- Oil & Gas (5)
- Pharmaceutical & Life Sciences (4)
- Industrial OEMs (3)
- Steel & Metal Manufacturing (3)
- Aerospace (2)
- Agriculture (2)
- Chemical & Petrochemical (1)
- Packaging & Processing (1)