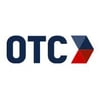
OTC Insights Team
Established in 1963, OTC Industrial Technologies (Ohio Transmission Corporation) is one of the largest industrial distributors & service providers in the United States. We're committed to seeing industrial operations advance through expert technical solutions & unmatched support using our years of experience.
Employees are the backbone of any company. Providing your employees with what they need to complete work efficiently starts with a safe environment. To that end, manufacturers have implemented standard safety practices such as mandating PPE (Personal Protective Equipment), visible safety signage, and job training.
The goal for manufacturers should be zero accidents. With the recent labor and workforce challenges, it is critical that you design a workspace where employees can feel safe. Companies are looking to increase safety standards even more. With that in mind, we have additional ideas and tips for increasing safety at your manufacturing plants.
Implement Additional Preventative Maintenance Measures
With preventative maintenance, a manufacturer will conduct repairs, perform calibrations, replace parts, and run tests on equipment or a machine. Often, these things are done as an afterthought and when it’s convenient, the bare minimum that is recommended by the OEM.
That can leave your equipment at risk of a dangerous failure, such as a vent that is clogged or a gearbox that is misaligned. Worse, it can put a worker at risk. Consider bringing in an outside resource that specializes in maintenance to review your machines and maintenance schedule. They can offer customized measures to increase the efficiency and output of your equipment. For example, a filter spec change in your finishing system, one that better suits your need, might reduce the need for maintenance or the presence of dangerous particulates in the workspace.
Utilize Robotics and Automation for Dangerous Work
Robotics and automation aren’t only a benefit for efficiency, but also safety. Repetitious work, like moving parts or tightening screws, can be physically hard for an employee. Identify tasks that can be physically taxing and see where a robot might complete the work more easily.
You can also use automation to complete work in dangerous areas. For example, rather than having an employee conduct a data check in a toxic environment, use a sensor. Sensors today can operate in extreme environments, so there is no reason to put an employee at risk. If you have questions about how to implement automation in your plant, reach out to OTC. Our automation team provides end-to-end service, from design to implementation to training. We can design the best solution for your needs.
Add Sensors and Light Curtains for Additional Support
Sensors and automation tools can also be used to support shop floor activities. For example, a small light curtain can warn employees when they are too close to dangerous machinery. With the use of RFID, you can set permissions on an employee badge. A sensor can be triggered when an employee without the proper training is entering an area they shouldn’t.
You can also use a simple automated checklist for certain things. This checklist can include a maintenance check — A machine won’t start until the checklist is signed off. It not only reminds the employee what must be done, but it also provides valuable data, supports maintenance procedures, and ensures that safety protocols are followed even in the rush of production.
Move Unnecessary Equipment Off the Shop Floor
Shop floor space is at a premium for many manufacturers. Adding another workstation or incorporating another product line can mean tighter working conditions. Employees must operate in extremely tight areas near potentially dangerous equipment.
There are ways to free up space on your shop floor. For example, MODULAIR® from OTC is a state-of-the-art housing unit for air compressors and dryers. It allows you to move the compressors from the shop to a pre-engineered building outside the facility. The building is designed for air compressors, making maintenance and management of the compressor easy.
Leverage Data Collection to Identify Problems
Data is one of your most valuable commodities once you start collecting and using it. After an accident, it is critical to identify the root cause (via a root cause analysis) of the incident. The goal is to not just identify the immediate contributing factors, but also the systemic and behavioral factors that led to the problem. With the right data, collected in real time, you can efficiently target those factors.
The true benefit of a root cause analysis isn’t just to identify problems, but to correct and prevent them in the future. Data can also help there. For example, if a certain machine in your shop causes accidents when it runs at a higher speed, you can set a threshold to keep it from running at that speed. A signal would let the operator know the machine needs to cycle down.
Contact OTC to Discuss Your Safety Needs
Ensuring safety is non-negotiable for manufacturers.
Today, with new technologies and best practices, companies can not only meet the minimum safety standards but exceed them. This effort will not only keep workers safe and your facility running, but you’ll also see efficiency gains and higher productivity.
Are you ready to streamline your data and work more efficiently? Contact OTC to get started.
Stay up to date
SUBSCRIBE TO OUR BLOGPosts by Tag
- General Manufacturing (99)
- Compressed Air Solutions (54)
- Automotive (35)
- Finishing and Dispensing (31)
- Rotating Equipment (27)
- Industrial Automation (21)
- Maintenance & Repair Services (20)
- Case Studies (15)
- Electronics & Semiconductor (14)
- Sustainable Manufacturing (11)
- Energy Efficiency (10)
- Filtration (8)
- Energy, Power & Utilities (7)
- Food & Beverage (5)
- Oil & Gas (5)
- Pharmaceutical & Life Sciences (4)
- Industrial OEMs (3)
- Steel & Metal Manufacturing (3)
- Aerospace (2)
- Agriculture (2)
- Chemical & Petrochemical (1)
- Packaging & Processing (1)