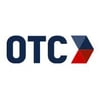
OTC Insights Team
Established in 1963, OTC Industrial Technologies (Ohio Transmission Corporation) is one of the largest industrial distributors & service providers in the United States. We're committed to seeing industrial operations advance through expert technical solutions & unmatched support using our years of experience.
In manufacturing, it is important to evaluate every step of your production process. By breaking down your operations, you can evaluate every phase of production to see where you are operating efficiently and generating profit.
You can also see where you have a problem.
The Profitability and Efficiency of Auto Finishing Operations
In this article, we’re going to look at practical ideas you can use to reduce costs and increase the profitability of auto-finishing operations. Implementing even one idea here can deliver a tangible ROI. It can mean a long-term benefit that boosts your bottom line with every order. Let’s get started.
Leverage Automation
Automation uses technology to control industrial processes and machines and has found beneficial applications in finishing. It's a way of completing work more efficiently.
For example, automation can be used to send work instructions to the finishing department. Rather than printing off the order details and clipping it to the traveler, a simple barcode scan on the order can pull up the instructions and load it into the finishing system. Completing an order can also be done with a barcode scan or an RFID tag so that as finishing is completed, the next step in the process is queued up and ready, whether it’s packing or additional assembly operations.
Implement Robotics
Related to automation, robotics in finishing can complete tasks and work that were once completed solely by human workers. There are several applications for robotics in finishing, and they offer powerful benefits to efficiency and cost savings.
Robotics is very good at precise and repetitious activities at the core of finishing. This can decrease waste and increase output in a paint booth, as well as reduce scrap for a mistake. In addition, a robot doesn’t need a break and won’t tire as it works, which means more uptime. While there are initial costs to adding robotics to finishing operations, there are also powerful benefits.
Conduct an Analysis of Current Systems
By partnering with an expert provider, you can have them conduct an in-depth analysis of your current systems to identify improvement opportunities. They can review the end-to-end process, looking at ways to increase efficiency or reduce costs. For example, the expert may suggest that changing to a different paint gun would reduce waste.
Your compressed air system is another area where an expert partner may be able to find opportunities for improvement. An analysis of your system may reveal problems. The right system can deliver the right amount, of moisture, pressure, or cleaner air which can mean less product scrap. Don’t assume your current finishing system is optimal. Work with an OTC expert to identify every opportunity for improvement.
Optimize Filters and Filter Efficiency
For many operations, the filter isn’t a top priority. Manufacturers will find a filter that works, set up a schedule for ordering and replacing them, then forget about it. But this may be costing you money or causing scrap and low-quality products.
Have an expert evaluate your use of filters. The wrong filter, or a low-cost filter inappropriate for your current use, can be expensive and hurt production efficiency. If the filter isn’t designed for your paint medium or is too small for your current output, you may be changing your filters more than you need to. They may not be filtering the air properly, causing an environmental hazard or a lower-quality finish.
Preventative and Predictive Maintenance
In the past, a maintenance plan for the paint booth could just be "fix it when you need to." Today, there are better options for maintenance. These include preventative and predictive maintenance.
With preventative maintenance, you conduct regularly scheduled maintenance on your equipment before a problem happens. Many, if not all, manufacturers already use some form of preventative maintenance, but it is worthwhile to evaluate your current maintenance standards for improvement. For example, if you see regular problems with the heating elements in the finishing booth, then it may be worthwhile to conduct a more thorough evaluation of that system.
Predictive maintenance takes it a step further by using connected equipment to collect and evaluate real-time operational data to optimize your maintenance protocols. A sensor on the line may detect vibrations that can trigger an alert that the line needs maintenance. It uses data to make cost-effective maintenance decisions.
Manufacturing Efficiency with OTC Industrial Technologies
In manufacturing, the decision with the highest risk is (too often) doing nothing. And yet, many companies do nothing when it comes to optimizing and improving their finishing operations.
If you have questions about your auto-finishing operations, then contact OTC Industrial Technologies. OTC offers true end-to-end solutions for finishing. From industry-leading filters to advanced air compressor solutions, to expertise in the latest automation and robotics, to paint booths and spray guns, we deliver solutions to the most challenging problems facing manufacturers.
Stay up to date
SUBSCRIBE TO OUR BLOGPosts by Tag
- General Manufacturing (99)
- Compressed Air Solutions (54)
- Automotive (35)
- Finishing and Dispensing (31)
- Rotating Equipment (27)
- Industrial Automation (21)
- Maintenance & Repair Services (20)
- Case Studies (15)
- Electronics & Semiconductor (14)
- Sustainable Manufacturing (11)
- Energy Efficiency (10)
- Filtration (8)
- Energy, Power & Utilities (7)
- Food & Beverage (5)
- Oil & Gas (5)
- Pharmaceutical & Life Sciences (4)
- Industrial OEMs (3)
- Steel & Metal Manufacturing (3)
- Aerospace (2)
- Agriculture (2)
- Chemical & Petrochemical (1)
- Packaging & Processing (1)