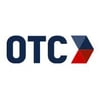
OTC Insights Team
Established in 1963, OTC Industrial Technologies (Ohio Transmission Corporation) is one of the largest industrial distributors & service providers in the United States. We're committed to seeing industrial operations advance through expert technical solutions & unmatched support using our years of experience.
Too often, manufacturers let equipment repair become an afterthought.
Basic machine maintenance is critical to smooth and efficient operations. Forgetting to review your equipment can leave you with a major problem. The filter you left in place a few days too long could cause a quality issue. A drill press running slowly puts you behind schedule with every operation.
With manufacturing equipment, each small problem can have an impact that quickly spirals out of control in your chain of production. A single delayed repair or missed maintenance check can lead to much larger expenses or worse, an overall production shutdown.
Make Your Manufacturing Equipment Repair Services an Operational Advantage
As a manufacturing leader, you need to ensure that your equipment and machines operate at peak efficiency. Think of it as a manufacturing service and repair strategy. That starts with making sure you have the right team in place to manage repairs and plan for maintenance.
Use a dedicated team or service for repairs, one that understands the unique needs of manufacturing equipment. Rather than relying on a part-time in-house team, look for specialists that have the training and expertise to make the most of every repair.
This will prevent future problems, make it more likely that you are taking full advantage of the time a machine is down, and help limit the overall cost of repair services. Because of their experience, they can cut down on the time for repairs, and provide insight that may increase the overall efficiency and uptime you see on the machine.
Tips for Developing Your Repair Services Strategy
As you evaluate your current repair services for manufacturing operations, use these tips to make the most of your maintenance and repair strategy:
Start with a System Assessment and Equipment Audit
Don’t make any decision on your equipment maintenance or repair until you conduct an audit of your current operations. Are you using the right filters for your finishing system? Are there leaks in your compressed air system? Is there a more efficient solution for your replacement parts?
Partner with a company that specializes in maintenance and repair. Have an expert visit for an on-site review of your equipment and operations. They can provide an outside perspective and additional insight, information, and data that you may not have.
In the long run, that data will be critical in developing your strategy.
Identify Potential Problems and Challenges
Once you’ve completed an assessment, create a list of potential problems. Identify the problem areas and work with your team to determine the cost (or potential cost) of these existing issues.
At this point, you can begin addressing them. Determine what changes you need to make now, whether it’s a change in replacement parts, an immediate repair, or an adjustment in how maintenance is currently handled. With an idea of the cost of these problems and the potential ROI, you’ll have the evidence you need to push these changes through. You can also start prioritizing work, tackling the most pressing issues first, and then addressing other problems as soon as possible. Best of all, you have the data to make the best decisions and keep your business running efficiently.
Keep in mind, the cost of production downtime always outweighs the cost of machine maintenance or purchasing backup equipment.
Implement Proactive Solutions
With the most immediate problems addressed, it’s time to start looking at the future and how you can begin to optimize. One strategy to consider is proactive solutions. For example, if there’s a machine that sees frequent downtime or costly repairs, consider using a vibration analysis system to detect when a problem starts. Work closely with your repair team to develop long-term, sustainable solutions to recurring problems.
Predictive maintenance is another option. Start collecting machine data and set baselines for efficient machine operations. When your equipment is running slower than it should, or experiences heat spikes, then look at conducting maintenance to identify problems early.
Don’t Hesitate to Use Alternative Equipment Repair Solutions
When you partner with the right specialist in manufacturing equipment repair, you’ll have additional options for service. Don’t hesitate to use them.
For example, a field service team may be able to handle a complex repair in the field, reducing the time required to get a machine up and running. It's less expensive than purchasing new equipment. Field service work is also quicker than waiting for new equipment to be delivered. Rental equipment is another option that can help prevent extended downtime.
Increase Efficiency and Production with Your Repair Service Solution
Efficient operations require efficient machines and equipment. Waiting to have a machine repaired, or letting your maintenance slip, can cause problems that put production at risk.
Without a strong repair and maintenance service partner, you may not even know the problems lingering and hiding in your equipment operations. For many manufacturers, these problems can lead to unexpected expenses, unacceptable downtime, and shipping delays.
If you want to discuss your production needs with a team dedicated to supporting manufacturers with expert maintenance and repair services, contact OTC Industrial Technologies today. We’re ready to help.
Stay up to date
SUBSCRIBE TO OUR BLOGPosts by Tag
- General Manufacturing (99)
- Compressed Air Solutions (54)
- Automotive (35)
- Finishing and Dispensing (31)
- Rotating Equipment (27)
- Industrial Automation (21)
- Maintenance & Repair Services (20)
- Case Studies (15)
- Electronics & Semiconductor (14)
- Sustainable Manufacturing (11)
- Energy Efficiency (10)
- Filtration (8)
- Energy, Power & Utilities (7)
- Food & Beverage (5)
- Oil & Gas (5)
- Pharmaceutical & Life Sciences (4)
- Industrial OEMs (3)
- Steel & Metal Manufacturing (3)
- Aerospace (2)
- Agriculture (2)
- Chemical & Petrochemical (1)
- Packaging & Processing (1)