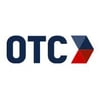
OTC Insights Team
Established in 1963, OTC Industrial Technologies (Ohio Transmission Corporation) is one of the largest industrial distributors & service providers in the United States. We're committed to seeing industrial operations advance through expert technical solutions & unmatched support using our years of experience.
Steel manufacturing is energy intensive. At first glance, there isn’t much opportunity for reducing energy use when you’re processing ore or melting and shaping steel. Energy efficiency in this industry isn’t easy.
But manufacturers see the business advantages in reducing waste and increasing efficiency. Going green is about working smarter, getting more done in less time, reducing waste, and having less impact on the environment.
How to Increase Efficiency in Steel Manufacturing
While science and technology continue to push what is possible in production, even for steel and metal manufacturing, there are steps companies can take even now to operate more efficiently and reduce energy costs.
Implementing one or two of these tips for energy efficiency in the steel industry can lead to a quick ROI for your facility.
Review Maintenance Procedures
Maintenance, especially for pumps and motors used in metal and steel manufacturing, can be an expensive and intense procedure. It can mean downtime and additional expense. However, waiting to conduct standard maintenance can lead to longer production delays and costly repairs. It can even lead to increased safety issues.
Schedule time to discuss the pumps and equipment you are currently using with a repair service or a service provider trained in the equipment to identify any opportunities for improving your maintenance procedures. Whether more regular but less intrusive maintenance, or a sensor that provides predictive maintenance data, these small changes can lead to efficiencies, higher output, and less waste.
Utilize Energy-Efficient Machines and Equipment
Today, equipment is more energy efficient than in the past, including equipment for the metals industry. There will be areas where you won’t be able to adjust, but taking advantage of more energy-efficient equipment will reduce costs. A monitoring system on your current equipment such as air compressors can adjust output as needed, reducing energy costs.
In manufacturing, compressed air generation is one of the highest energy expenses. Switching to a more efficient compressor, like an oil-free system or even a compressed air utility service like DIRECTAIR®, can have immediate benefits by lowering energy consumption, increasing efficiencies, and reducing overall costs.
Leverage Automation
Automation and robotics have come of age in manufacturing. Steel and metals manufacturers are already leveraging robotics, but there are further opportunities to increase efficiency. For example, look at how the finished product is moved to the warehouse. Rather than using a diesel lifter, an automated system may save both time and energy costs and potentially reduce the risk of injury.
Custom fabrication may also provide efficiency opportunities at your facility. Schedule time with an automation expert to review your processes. They will provide additional insight and opportunities. You may not use every idea they provide, but over time you can continue to refine and optimize your operations.
Review Finishing Operations
Finishing is critical in metal manufacturing. Inefficient processes can often lead to waste and increased costs. Work with finishing experts who can streamline and optimize your processes to deliver the highest-quality results while reducing waste.
Compressed air is commonly used in finishing. We discussed using more efficient air compressors or even a compressed air utility service to reduce energy use. In fact, many services can provide as much as 35% to 50% energy savings.
Data for Better Decisions
With the data available to manufacturers today, there’s no reason you shouldn’t implement more data-driven production decisions. This includes predictive maintenance on critical equipment. As you begin to connect more of your equipment to a central repository for data, you can begin to set baselines for efficient operations. Take steps to address problems as your equipment deviates from the baseline.
Look at also providing your frontline production team that data. Rather than sharing it at a morning meeting or compiling it in a report, provide it to your production team in real time. Let them know when a machine is operating but has additional capacity. Let them know when a machine is running hot, or fast, so they can adjust to reduce waste.
Optimize Your Steel and Metals Manufacturing
There is no perfect answer to green initiatives and energy efficiency in your steel and metals manufacturing business. But there are steps you can take to cut down on waste and energy use while improving output. The sooner you start taking those steps, the larger the ROI you’ll see for your business.
If you have questions or want to discuss your options with a team of cross-disciplinary experts who understand manufacturing and production, then contact OTC Industrial Technologies. We know manufacturing and have the experience to make a difference for you.
Stay up to date
SUBSCRIBE TO OUR BLOGPosts by Tag
- General Manufacturing (99)
- Compressed Air Solutions (54)
- Automotive (35)
- Finishing and Dispensing (31)
- Rotating Equipment (27)
- Industrial Automation (21)
- Maintenance & Repair Services (20)
- Case Studies (15)
- Electronics & Semiconductor (14)
- Sustainable Manufacturing (11)
- Energy Efficiency (10)
- Filtration (8)
- Energy, Power & Utilities (7)
- Food & Beverage (5)
- Oil & Gas (5)
- Pharmaceutical & Life Sciences (4)
- Industrial OEMs (3)
- Steel & Metal Manufacturing (3)
- Aerospace (2)
- Agriculture (2)
- Chemical & Petrochemical (1)
- Packaging & Processing (1)