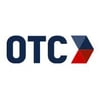
OTC Insights Team
Established in 1963, OTC Industrial Technologies (Ohio Transmission Corporation) is one of the largest industrial distributors & service providers in the United States. We're committed to seeing industrial operations advance through expert technical solutions & unmatched support using our years of experience.
Compressed air is an essential resource for manufacturing.
Without a steady supply of clean, dry air, production can suffer. Rental air compressors help ensure that you always have access to the compressed air you need. Whether you’re replacing a broken compressor or dryer, or just want to test a new unit before purchasing, rentals are a cost-effective option that can be an integral component of your production strategy.
How Do Manufacturers Use Compressed Air?
In almost every manufacturing vertical, compressed air can perform a variety of functions.
Compressed air is used to control the spray of paint nozzles, operate pneumatic tools and pumps, for cooling and heating applications, cleaning, and in many other ways. With so many applications, a broken or hindered air compressor is a potential production disaster. Rather than struggle with extended downtime or an inconvenient workaround, a rental strategy can prevent problems and keep production flowing.
How Can Air Compressor Rentals Help Overcome Manufacturing Challenges?
There are similarities between purchasing a new air compressor and renting one.
Just as if you’re purchasing a new air compressor, it’s important to find the right model and to work with a knowledgeable supplier to help maximize your investment. Replacing your existing machine without significant disruption isn’t always easy, so working with a team that understands your situation can help you get the best results.
Here are a few ways the OTC team can help you overcome manufacturing challenges.
1. Keep Your Business Running During Emergencies
When a compressor breaks down, the clock starts ticking. Every minute of lost production puts you further behind in your manufacturing goals and makes it harder to keep your promises to customers. Rental compressors provide the fastest solution to getting your facility up and running. They are easy to install and, with the right rental provider, one with plenty of machines on hand and a team experienced with compressed air and quick installation, the shop floor will see little difference with the rental unit. It can provide either a stopgap measure or a longer-term solution as you evaluate your compressed air needs.
2. Work Within Budget Constraints
Producing high-quality products while reducing costs isn’t easy. Your budget can’t always handle the strain of additional capital expenses when you find yourself in a situation where you need a new compressor. Renting an air compressor not only helps you stay under budget, but it allows you to work with the latest machines on the market. It is often easier to budget for a rental unit than to invest in a new machine (and all the repairs and maintenance that may come with it). Make sure to include rental air compressors in your long-term facility planning.
3. Reduce the Impact of Planned Maintenance
Even the best compressors require maintenance and upkeep. Planned maintenance helps you get the best performance out of your compressor, but production can suffer during these extended repair windows. This is especially true of larger high-capacity and high-pressure air compressors that require extensive maintenance. If you know you have planned maintenance scheduled, then coordinate the work with a rental supplier to ensure you have the right rental equipment on hand. Don’t let your essential maintenance hold you back — find a solution that reduces downtime.
4. Easily Handle Surges in Production
In manufacturing, there will be spikes in production. If your air compressors are operating at or near maximum capacity, then additional work can put a dangerous (and potentially costly) strain on your equipment. Rather than put your equipment at risk, rely on rentals to handle the additional work. Many businesses experience production swings based on the season, so planning for increased demand helps you stay ahead. Schedule to have rental units available for additional orders. If your current compressor is a production bottleneck, then don't fall behind on orders before you bring on a rental unit.
5. Try Before You Buy
Sometimes you don’t know whether a certain model is right for your facility until you try it out. Purchasing a new air compressor can be stressful, as buying the wrong machine leads to a variety of logistical problems. If you want to confirm that a machine will work with your existing operation, then a rental can verify your assumptions. Renting an air compressor allows you to test output requirements, the humidity and the cleanliness of the air, and other factors. Many manufacturers still aren’t sure if oil-free compressors are the best choice. Rent an oil-free compressor to confirm it will meet your output needs with cleaner air and operations.
Discover All the Ways OTC Can Help
Rental air compressors should be a critical part of your production and maintenance strategy. Get ahead of problems by scheduling a rental unit before conducting maintenance. Plan for the unexpected by reaching out to a trusted rental supplier like OTC before a disaster occurs. Taking the time now to prepare, before a problem happens, will save you time, money and stress in the future.
Want to learn more about OTC’s rentals, or perhaps discuss your needs or look at an air compressor update? Contact us today to speak to a member of our team. We want to learn about your unique situation so we can provide you with the best machine for the job.
Stay up to date
SUBSCRIBE TO OUR BLOGPosts by Tag
- General Manufacturing (99)
- Compressed Air Solutions (54)
- Automotive (35)
- Finishing and Dispensing (31)
- Rotating Equipment (27)
- Industrial Automation (21)
- Maintenance & Repair Services (20)
- Case Studies (15)
- Electronics & Semiconductor (14)
- Sustainable Manufacturing (11)
- Energy Efficiency (10)
- Filtration (8)
- Energy, Power & Utilities (7)
- Food & Beverage (5)
- Oil & Gas (5)
- Pharmaceutical & Life Sciences (4)
- Industrial OEMs (3)
- Steel & Metal Manufacturing (3)
- Aerospace (2)
- Agriculture (2)
- Chemical & Petrochemical (1)
- Packaging & Processing (1)